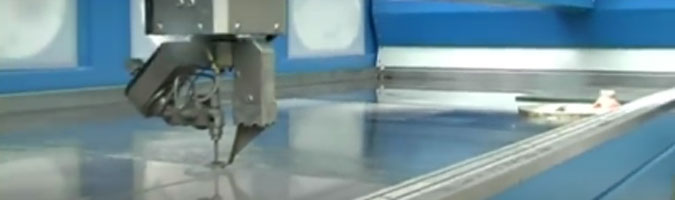
Even though waterjet cutting has only come into its own in recent years it may surprise you to know that it has been around since the 1930s. At that time it was used at a low pressure and only for cutting soft materials. Whilst things continued to develop after the war, waterjet cutting became much more effective in the 1970s, when the first reliable high pressure pump was developed.
Whilst the earlier waterjet machines could cut softer materials they could not handle harder materials and metals. The ability to cut harder materials like metal came about following the addition of an abrasive to the waterjet cutting nozzle. This was a technique first used in the 1930s, however early versions of the nozzle were not commercially viable. Further development of the nozzle and the availability of a reliable pump led to a more effective waterjet that could now cut through a bigger variety of materials.
How does Waterjet Cutting work?
The ability to cut materials is obtained by pressurising water to extremely high levels and then feeding that water stream through a small orifice
- The normal tap water feed is pressurised by the pump
- The water is forced through the orifice, forming an intense cutting stream
A separate mixing chamber in the body of the cutting head is where abrasive is mixed with the water to allow cutting of harder materials. The fact that this facility is in the chamber head means that it can be turned on and off easily, making the change between cutting hard and soft materials quick and effective.
There are a number of advantages of using waterjet cutting over other methods, the most important of which is the ability to cut materials without heat. This means there is no heat affected zone and so no interference with the material structure or property and no impact on tensile strength.
What materials can be cut?
There are a whole range of materials that can be cut using this method with tempered glass being the only material that seems to have problems. Otherwise, almost anything else can be cut. Soft materials like paper, sponge, rubber and plastics, even re-inforced ones can be cut. Wood, of course and most steels and alloys can be cut, including titanium. Stone, concrete and ceramics are fine, and yes, glass too.
However, you also have to factor in the thickness of a material when considering how practical and cost effective a project will be. For instance, you can cut through 60cm of foam or rubber much more quickly than 60cm of concrete. If cutting metals, the thicker the material the longer it will take to cut.
This article in engineering.com has a useful graph of cutting speeds from slowest to fastest for any given constant material thickness.
PRV Engineering use the Idroline S1730 hydro-abrasive waterjet cutting system at their Pontypool based premises. It is just one of a vast array of services offered using state of the art CNC Multi Axis / Multi Discipline machining centres.
This site uses Akismet to reduce spam. Learn how your comment data is processed.
Leave a Comments