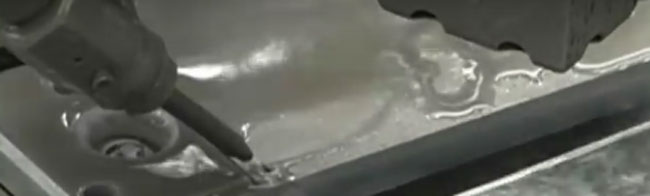
There are many advantages of waterjet cutting compared to other methods, but if we had to try and summarise them neatly into a few words we’d say;
The ability to cold cut almost any material in any direction with less waste and a superior finish.
But really that’s not enough of an explanation, so let’s expand a little on that statement and address some of the areas of improvement over more traditional cutting methods.
Omni-directional cutting
Waterjet cutting allows omni-directional cutting – the ability to cut in any direction which gives much greater cutting flexibility. In most cases starting holes are not required as the water jet is able to perforate the material. It is now much easier to cut more complex shapes and designs into all sorts of materials.
Cutting width
The small kerf (or cutting width) allows for much better material utilisation. Raw materials can be expensive or there may be a limited resource. Better use and optimisation of the material can result in less being used and an increase in cost effectiveness.
Cold cutting
Cold cutting means there are no heat affected zones and no hardening of materials. More traditional cutting methods struggle with heat sensitive materials. Heat around the cutting area can cause burning to some materials and also have an impact on the tensile strength of the finished product. Cold cutting takes this away.
Stress free cutting
This doesn’t mean the machine takes the stress from the operator, although you could argue that in some ways it does! No workload on the material (as is the case with other methods) means no stress on the cut.
Improved finishing
All of the above result in finished part production in most cases. In most cases there is no secondary processing needed.
Quicker than conventional cutting methods
As there are no oils, emulsions, gas changes etc. needed, changes in materials can be handled much more quickly
Environmentally friendly
Other cutting methods can result in dust, chippings or hazardous gases. Normally waterjet cutting removes this.
PRV Engineering have added waterjet cutting capabilities to their diverse range of services. The Idroline S1730 hydro-abrasive waterjet cutting system is the latest addition to the suite of state of the art CNC Multi Axis / Multi Discipline machining centres and allows us to continue to improve and provide the best service to our clients. We manufacture across a variety of industries and the addition of waterjet cutting facilities ensure that as client requirements become more complex, we are able to meet them.
This site uses Akismet to reduce spam. Learn how your comment data is processed.
Leave a Comments