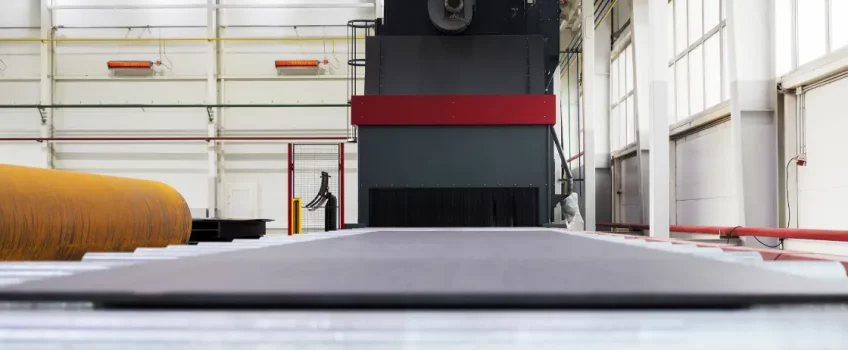
When it comes to finishing and cleaning operations, shot blasting is one of the most effective methods for surface treatment. It is a technological process used to remove various impurities from different surfaces using abrasives. In this article, we look at a few different shot blasting techniques, applications, and pros and cons with some additional FAQs at the end.
What Is Shot Blasting?
Shot blasting uses high-velocity steel abrasives in a controlled manner to treat the surface of a metal object. These high-speed controlled blasts create an abrasive impact which removes any surface contaminants, making it an effective method for cleaning iron, steel, forgings, machine parts and fixtures among others. Shot blasting is ideal for cleaning and preparing surfaces for painting or other finishes but not all methods are the same.
Shot blasting uses several types of metal abrasives from steel grit and copper shots to aluminium pellets. Other shot blasting methods include using silica sand, glass beads, synthetic materials (sodium bicarbonate) and agricultural materials like crushed kernels.
Primary Abrasive Shot Blasting Methods
- Micro-abrasive blasting is a dry technique using a small nozzle to direct a fine stream of abrasive material to a targeted area.
- Bead blasting uses glass beads to remove surface deposits, ideal for cleaning fungus, paint and calcium deposits.
- Wheel blasting is an airless technique using centrifugal force to shoot abrasives against a surface without a propellant.
- Hydro blasting or water blasting uses high-pressure water to remove paint, chemicals and build-up of debris.
- Wet abrasive blasting uses cold or hot water to remove grease, dust and hazardous materials. Operators can also add detergents to the water to further improve cleanliness.
- Dry ice blasting technique uses air and dry ice to remove items from a surface while it also decontaminates.
- Bristle blasting uses a high-carbon rotary steel brush that prepares a surface.
- Vacuum blasting generates very little dust and spills as it uses dry blasting methods and collects blast media simultaneously.
Did you know?
Shot blasting is one of the most effective and perhaps the cheapest methods for surface preparation. It leads the field ahead of processes such as galvanizing, electroplating, welding, enamelling, glass coating, and rubberising.
Shot Blast Machines: Types of Abrasive Delivery Options
Shot blast techniques use two different methods of propelling the steel shot. The criteria for choosing the right technique will be based on the area of application, such as surface condition, final finish specifications, etc. Here are the two abrasive delivery options you can choose from.
Compressed Air (Pneumatic)
The option is perfect for projects with a lower production rate. This machine uses compressed air to accelerate steel shots which can be directed horizontally, making this an excellent choice for finishing welds and frames made of steel. As a result, it all but eliminates the need for hand tools altogether!
Centrifugal Turbine
The centrifugal wheel technique is a more common and economical option for finishing and cleaning. It propels abrasive shots in a specific direction at a controlled speed using a centrifugal turbine. The power of the centrifugal turbine used in this type of blasting machine will depend on the degree of cleaning required.
Benefits Of Shot Blasting
Since shot blasting cleans surfaces better and faster than traditional techniques, here are some of the major benefits.
- It eliminates the use of dangerous chemicals
- It provides higher production rates, wider abrasive selection and better blast pattern accuracy
- The finished surface is free from chemical deposits, scales and dust
- It facilitates the formation of a permanent bond between the protective coating (zinc, paint or epoxy) and the blasted surface.
- It helps detect surface faults or defects
- It also increases the longevity and durability of protective surface coating as it adheres better to the cleaned and scale-free surface
Which Industries Rely On Shot Blasting?
Shot blasting is most commonly used in aerospace, automotive, construction, shipbuilding and rail among many others. It is used to remove rust, paint, and other contaminants from metal surfaces. It can also be used to prepare surfaces for painting or coating. In the automotive industry, shot blasting is used to clean engine parts and body panels. It is also used to prepare surfaces for welding, which is one of many services PRV Engineering provides.
What Are The Disadvantages Of Shot blasting?
While, a highly effective method for removing contaminants from surface areas, there are also a few downsides. The process can be messy and dusty and dangerous. If it’s not performed correctly, it can also damage the surface of the metal.
What Is Sand Blasting?
Sand blasting is a type of abrasive blasting that uses sand to remove contaminants from surfaces. It is a fast and effective way to clean surfaces, but it can also cause damage if not done correctly.
What Is Shot Peening?
Shot peening is a process that uses small metal pellets to remove contaminants from surfaces. It is a gentler process that doesn’t damage the surface of the metal but it’s not as effective at removing heavy contaminants as other shot blasting methods.
Is Shot Blasting Safe?
Shot blasting can be dangerous if not done correctly. Always wear proper safety gear, such as gloves, eye protection, and a respirator. Never point the nozzle of the shot blaster at yourself or anyone else. Keep the area well-ventilated to reduce the risk of inhaling dust and contaminants.
If you’re looking for a reliable, reputable and highly capable shot blast company? As one of the leading companies in the CNC and shot blasting services industry, PRV Engineering provides engineering solutions of the highest standard. Equipped with state-of-the-art shot blasting machines, we can provide you with the right finish for your product. Visit the website for more information.
[…] more informative and interesting articles on waterjet cutting, CNC machining, shot blasting and emerging technologies, please read our blog and follow us on social media. You can also find […]