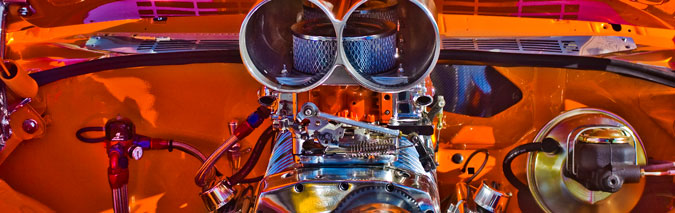
When it comes to manufacturing parts or components the way each one is finished reflects the quality of workmanship. If you don’t finish a job properly, then it doesn’t matter how careful you’ve been with the initial production, cutting or moulding, the end product is not going to look good. And the way the end product looks will always have an impact on saleability.
There could, of course, also be an impact on your costs. If your customer is unhappy with the finish of an order, you may have to start all over again, meaning more waste and increased costs. And there’s the health and safety aspect of poor finishing. Rough or sharp edges won’t be acceptable to your customer and may also cause injuries to those working with them.
So, finishing a job properly and professionally is just as important as the rest of the production process. However, the finishing is not just about the look of the end product. The main reason for finishing an item is to prevent corrosion or ensure conductivity, and choosing the correct coating is key if you want to get the maximum lifespan from the item.
Improvements in equipment mean that in some instances there is far less preparation for a finishing coating than there used to be. Water jet cutting systems are an example of this. The improved cutting widths and directions combined with the ability to cold cut means that in most cases no secondary processing is needed.
Where more finishing is required, preparation of the material (smoothing and polishing) is just as important as the choice of coating if you want to obtain the best results.
Here at PRV Engineering we like to provide the same excellent level of customer service and finish to all parts of any project and that can’t be done if you sub contract the final part of the process. It was for that reason we decided to have our own in house finishing department. As well as the standard types of coatings, as a major manufacturer of busbars we also provide a range of specialist coatings that provide additional insulative or conductive properties to products. These are applied by fluid bath, electrostatic spray or by simple heat shrink processes.
Our finishing department comprises of a 6m shot blast room and various shot blast cabinets, a powder coating booth, wet spray room and a 2.2m cubic high bake oven.
As well as having our own finishing department we have the means to test the finishes to ensure the highest quality to our clients. We can test for
- Gloss level
- Coating thickness
- Adhesion strengths
- Porosity
- Colour shade
- Dialectric strength
- Insulative or conductive properties
PRV engineering provide a wide range of services across various industry sectors and our multi discipline true one stop shop attitude means we are able to provide a complex and diverse range of products and services to our customers that allow them to satisfy their requirements from a single source.
Have a difficult or complex requirement? Get in touch. Because of our diverse range of services and skills we can often manufacture to unique requirements, whether it’s a one off or a large batch order.
Image credit: Aaron Barnaby
This site uses Akismet to reduce spam. Learn how your comment data is processed.
Leave a Comments