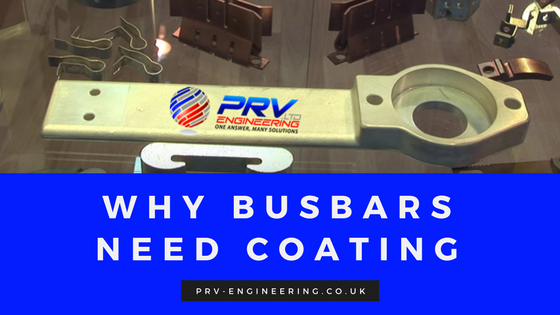
Busbars are astonishing pieces of technology that make complex power distribution simpler, more affordable and flexible. Different coating or plating materials provide varying levels of conductivity and duration of the product’s lifecycle.
Busbars are typically made from corrosion resistant copper, brass or aluminium in solid or hollow tubes. They are produced in a range of shapes including flat strips, solid bars and rods. Some of these shapes allow for more efficient heat dissipation due to high surface area to cross-sectional area ratio. Copper oxidises over time and without coating, more power is needed to push electricity along the surface.
Reasons for coating Busbars
-
To Inhibit Corrosion
Copper is generally corrosion resistant but in extreme environments with high humidity and rich in ammonia and Sulphur, additional protection is needed.
Metal coatings
Your choice of coating material could also depend on whether your busbar parts are moving or fixed. Tin-lead coatings are not used as often due to environmental concerns and should be avoided. Same applies to pure tin coatings as it forms whiskers and can cause transient short circuits.
Nickel and silver coatings are the preferred options as it’s relatively inexpensive and durable with a harder surface area. On the negative side, it corrodes significantly when in contact with metals like gold. Silver is the most effective option but also the most expensive and does not perform very well with Sulphur compounds.
Whichever metal you decide to use, an anti-tarnish finish is recommended to keep the surface clean and conductive for increased longevity and safety.
Non-Metal Coatings
Powder coating is a popular choice for insulating thick conductors, as well as conductors with multiple electrical contact points. It gives the ability to coat the busbar by almost ‘melting’ paint over the surface. This provides a durable protective layer which not only protects against corrosion but carries good insulation ratings. Powder coatings can be applied by electrostatic spray or fluid bath and then cured by heat-shrink processes or UV light.
-
To Increase Current Rating
It’s been suggested that matt black paint should be applied to busbars to improve emissivity. The matt black coating emits heat better from the surface than most others. However, the difference is not overly impressive and can in fact reduce the efficiency of the convection process. It is mostly used on wide busbars with high temperatures where the radiation is more effective.
-
For Cosmetic Purposes
More often than not, finger marks or typical handling smudges may occur during assembly. The natural grease in the marks darkens quicker than the surrounding copper and can be seen as dirty.
Some companies have no technical reason to paint busbars other than to hide marks. This can in fact hinder maintenance, increase working temperature and it costs extra. In some cases, the local market requires busbars to be painted which leaves the manufacturer not much of a choice.
Why PRV Busbars is the first choice for many
As part of our Busbar manufacturing services we provide a range of specialist coatings that provide additional insulative or conductive properties to the product. PRV Engineering specialises in the use of Copper to manufacture all manner of components for the Low, Medium and High Voltage Industries including Rail Rolling Stock and Trackside electrical components.
Below are just some of services we provide our clients in the Electrical Industry, all under one roof:
- Punching and Folding
- Forging and Pressing
- Complete Machined Castings and Stampings
- Busbar Fabrication
- Plating and Heat Shrink Sleeving
PRV has been a stable and profitable Busbar supplier, working in partnership with our customers to deliver a first class service. We have the skills, knowledge and experience to manufacture your replacement Busbars to order. Not only do we offer impeccable quality services, our clients get value for money unmatched by the original manufacturers. As a company, we can meet all your requirements in terms of busbars, conductors, copper contacts and connections.
To further improve customer service, we have our own plating facility and finishing department. It includes rooms and cabinets for shot blasting, spray painting booths, wet spray room and a high bake oven.
Please post a comment below or contact us via the website if you have any interesting stories or would like more information. You can also find us on Twitter, Facebook, You Tube, Google+ or LinkedIn.
This site uses Akismet to reduce spam. Learn how your comment data is processed.
Leave a Comments