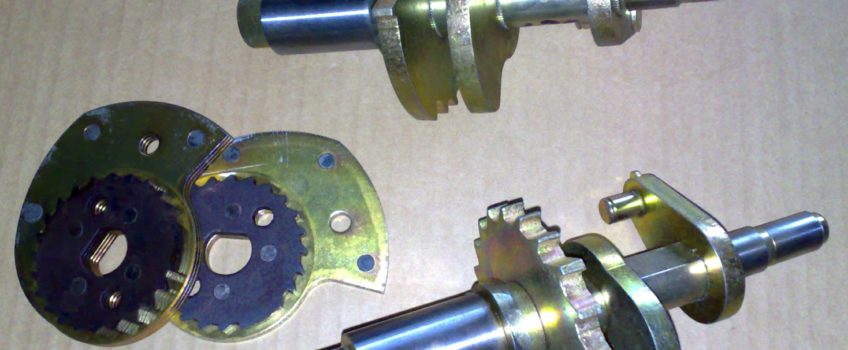
New Rapid Prototyping Development will Cut Costs and Lead Times
A new rapid prototyping development has been announced that could make the so called “rapid prototyping” process even faster. The new methodology revolves around making prototypes using vacuum forming technology. Vacuum forming is a way of thermoforming plastic. It involves manufacturing a tool, around which a heated sheet of plastic is draped. A vacuum is then created between the mould tool and the draped, preheated plastic. This vacuum sucks the heated plastic forcibly onto the tool, and holds in place whilst it is rapidly cooled by engaging the fans built into the vacuum forming machine. As it cools, the plastic conforms to the exact shape of the mould tool.
New Mould Tool Technology
The new rapid prototyping breakthrough comes from the way that the mould tool is manufactured. Up until now, the manufacturing time needed to produce a tool with the exact profile and dimensions would certainly be many hours. In some cases, (using resin, or fibre-glass tools for example), it would take days in order to carefully layer the materials, and to allow them to set. In the case of solid metal tools, many hours are needed to machine a block of metal down to the required shape and size.
Rapid Prototyping in Minutes not Hours
However, a new mould tool construction method has created a real leap forward in rapid prototyping timing for items whose size and shape are conducive to being vacuum formed. Instead of starting out with a solid block of metal, or a core which is then over-laminated, the new construction method uses a number of moveable pins. These moveable pins can be configured in any height and combination, thus allowing a shaped contour or profile to be created. With the aid of a CAD program, new rapid prototyping tools can be made in 18 minutes.
Rapid Prototyping Proves Feasibility
But what is even more important is that a tool can be reconfigured by resetting the adjustable pins. Prototyping often reveal mistakes or imperfections that need to be corrected before an item goes into full production. It’s actually what prototyping is all about; proving something before committing it to bulk manufacture. Under the old system of tool construction, the tool would have to undergo costly, time consuming modifications. But with the new adjustable pin method, modifications can be done much more quickly and therefore much more cost effectively.
Still in Development
This new rapid prototyping technology is still in the development stage. The system uses 2mm pins that are aligned and positioned from CAD fed data. Once the pins are in position, they are locked into place and then covered in a smooth silicon or neoprene material. This covering ensures that the mouldings that are pulled off the tool are blemish free.
Making it Affordable for the Engineering Industry
This new rapid prototyping research and the initial trials have been carried out by Brunel University. The present equipment weighs some 20 tons and costs millions. However, given the enormous impact that the new tooling methodology could have on the speed and cost of rapid prototyping, the research team are confident that it will be made more affordable for general use within the engineering community in the near future.
This site uses Akismet to reduce spam. Learn how your comment data is processed.
Leave a Comments