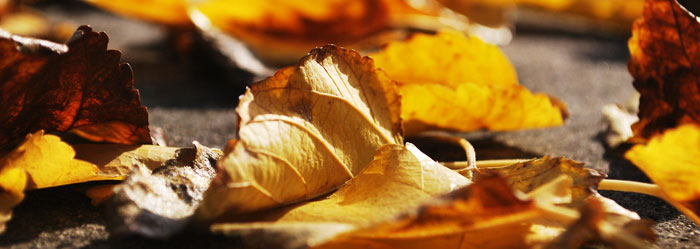
The weather has turned positively autumnal with a drop in temperature and leaves starting to drop from the trees. At this time of year commuters across the country groan and begin to think about how often the weather is likely to disrupt their daily journey to work. Leaves on the track is frequently put forward as the major reason for causing seasonal disruption to services on our rail network, and whilst at face value the reason sounds a little far-fetched, leaves on the track are in fact, a real safety hazard.
So why do leaves on the rail network cause so many problems? There are 2 key areas where leaves cause problems:
- Trains lose their adhesion as the rails become more slippy
- Leaves act as an insulator and can disrupt electrical signals on the track.
Tonnes of leaves fall onto the rails each year and as trains run over them they are ground down and create thin slippery, Teflon like layers on the track. In the same way that cars have to take care in slippery or icy conditions, once that layer is on the track trains also have to allow longer breaking distances. They also have to avoid accelerating too quickly to avoid wheel spin. Both things result in arrivals and departures taking a little longer and ultimately can cause delays in areas where the problem is particularly bad. If each train arriving and leaving has to do it a little more slowly, gradually it builds up and you have a general overall delay.
The leaf mulch can also act as an insulator interrupting signals from the train to the track. Signal systems use electrical currents from the track and when the mulch causes interruption, longer gaps between services have to be introduced to maintain safety. Again, during the day, these gaps, although individually small, all build up to cause longer delays.
Services like Network Rail have multiple things in place to try and prevent as much disruption as possible, but inevitably they are always fighting to keep up with or stay just ahead of the weather and the resultant problems. Many things are in place to help; track cleaning, application of additional adhesion materials to help grip and better braking systems are a few of the solutions.
Maintenance of the vegetation around the rail network is also an essential part of solving the problem. Planting of vegetation that isn’t likely to drop leaves can help.
In addition projects to develop improved solutions are ongoing with rail industry specialists and universities.
One such project is pioneering a microwave system from UK based company Imagination Factory. They have designed a system that fits cables to the front of train wheels that give off bursts of microwave energy, the idea being to dry the contact area between the rail and the wheel. Tests have only been conducted at slow speed to date but calculations indicate that the process will work up to speeds of 50mph. Full trials will take place on a test track in the west Midlands over the coming months. If successful it is hoped the system could be introduced into the rail network by 2019.
The project has been funded by the Rail Safety and Standards Board (RSSB) as part of the Predictable and Optimised Braking Challenge.
PRV Engineering work closely with the rail network manufacturing busbars, providing high voltage switchgear, manufacturing for track, track laying and maintenance equipment and also electrical connections, contacts and other rolling Stock product. We work closely with other companies providing overhead line equipment and so have a successful alliance with the rail network and its suppliers.
This site uses Akismet to reduce spam. Learn how your comment data is processed.
Leave a Comments