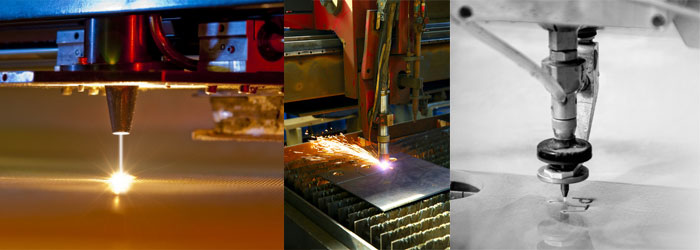
When you work in manufacturing you have a decision to make; laser, plasma or waterjet cutting? ‘Which one is best?’ is the first question that many people ask. The most up to date and technologically advanced must be the best, surely? Well that’s not the case. In fact there could be a case for using any or all 3 of the manufacturing processes depending upon your needs and what you value most from the machine.
Each has its own advantages and disadvantages, from speed to cost and even waste. So let’s take a look at each option.
Laser cutting
Laser cutting works by melting, burning or vapourising the material. A laser beam is reflected by mirrors which focus it onto the material for cutting. The fact that it uses a beam means that it can be very precise. It can be used on many materials as long as they are not reflective but does lose some of its accuracy when materials are thicker. You may also encounter problems with laser cutting where materials are composite, especially if they have different heat tolerances. Laser cutting does have a heat affected zone, which can cause fractures and disruption to materials. Whilst laser cutting can be quick, accurate and reliable, the heat affected zone and inability to cut reflective materials can be seen as a disadvantage. In addition it has a high power consumption and so can be costly to run.
Plasma cutting
In this method compressed gas is blown through a nozzle at the material being cut. Like the other methods it can cut quickly and effectively through most materials although it is not deemed to be as accurate as laser or waterjet cutting. In addition, when you cut different material it does require a change of cutting edge so is not as versatile as other cutting methods. One of the plus points of plasma cutting is that machines tend to cost less than laser or water jet machines and has a decent hole quality. A few of the main disadvantages are that it is less accurate, can produce poor edging on finished products and also produces fumes in the cutting process. Care does need to be taken regarding health and safety. Like laser, it also has a heat affected zone which can cause problems with different materials
Waterjet cutting
High pressure water jets are pushed through a nozzle to cut the materials. For tougher metals an abrasive material is added to help the cutting. Waterjet cutting is highly accurate and effective on any material. No heat affected zone means that there is no danger of disruption or fracturing to materials and so composite materials are cut just as easily as others. It can cut thicker materials but obviously the thicker the material the longer it can take. There is no hazardous waste, fumes or chippings with waterjet cutting. In addition the small kerf (cutting width) means as that there is much less general material waste which can result in cost savings. An excellent finish also means very little or no rework. Waterjet cutting can be seen as an expensive option as machines cost more than the alternative methods and cutting can be slower on thicker metals. They are also noisier in operation than the other methods.
So, when it comes down to making a decision over the machine to use, you have to decide what is best for your business. Cost, accuracy, types of materials being cut and general operating costs all factor.
Here at PRV Engineering we made the choice to use waterjet cutting. It is not the cheapest method but it is the most accurate, and for us that is essential to providing the best customer service. It also gives us the versatility and flexibility we need for manufacturing parts in any type of material.
Using waterjet cutting we are able to provide a sustainable, quality assured product every time.
This site uses Akismet to reduce spam. Learn how your comment data is processed.
Leave a Comments