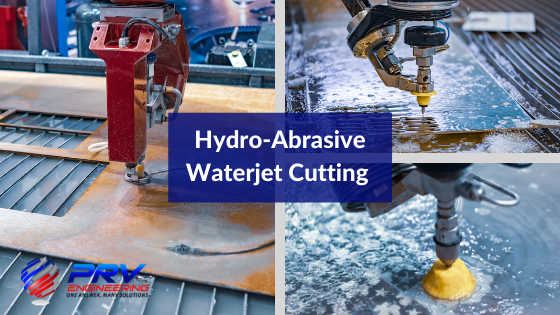
It offers customers a unique combination of flexibility, simplicity and precision unparalleled in other available technologies today. The small cutting widths and omni-directional cutting mean the machines can cut virtually any material with exceptionally high precision. Waterjet cutting offers extreme accuracy with tight tolerances and is especially suited to composites.
How Does Waterjet Cutting Work?
A waterjet cutting machine is a tool capable of slicing metal, or other materials, using a high velocity, high-pressure jet of water. You could compare the process to water erosion found in nature but with these machines, it’s significantly accelerated and concentrated.
It can also use a mixture of water and an abrasive substance to help cut tougher materials. With the right attachment to the cutting head, you can cut any layered or laminated composite material without delamination. This will ensure that the structural integrity of the material remains intact. It can cut a thickness of 1mm to 150mm in various sizes from the most intricate up to a 4m x 2m profile.
Related: ‘What Is A Waterjet Cutter And How Does It Work?’
What Does It Take To Cut Through A Material?
Unlike a thermal cutting process, such as plasma, oxyfuel, or even laser, waterjet cutting is a mechanical sawing process. Think of it like a band-saw where a thin strip of metal with sharp teeth are pulled through the material being cut. Waterjet cutting involves a thin, powerful stream of water with sharp pieces of rock. It’s these particles that are pushed through the material as a result of the high pressure.
The abrasive is usually made from crushed garnet but some applications use other materials, including olivine. This is a softer abrasive which is often used when cutting aluminium. However, garnet is by far the most commonly used abrasive for metal plate cutting. Each grain of abrasive that passes through the target object will wear away bit-by-bit until it meets the specified requirements.
Is There Anything A Waterjet Can’t Cut?
Due to its unique characteristics, a waterjet can cut all sorts of composites such as carbon fibre reinforced plastics, glass-reinforced plastics and almost any metal. In fact, the most common application in machine shops is metal, especially aluminium.
There are, however, a few exceptions and that includes tempered glass as it’s too fragile for any machining process. It will shatter if cut or broken which is why it is frequently used in windshields. While it can cut most materials, accurate profiles are not possible on diamonds, cast iron, talonite, stellite and advanced ceramics.
In some instances, composite materials (layers of different materials) can’t be cut because the water will seep between the layers and “delaminate” the material. That said, waterjet cutters can handle most composite materials just fine.
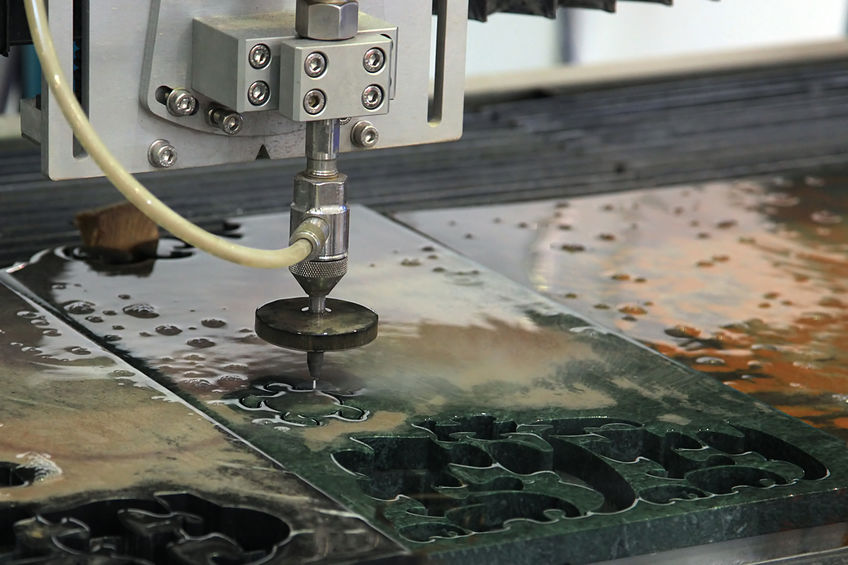
Advantages Of Abrasive Waterjet Cutting
Waterjet cutting is often used when fabricating machine parts and a common sight in mining and aerospace for cutting, shaping and reaming. There are countless benefits to waterjet cutting including the ability to cut heat-sensitive material which eliminates the risk of adding material stresses generally associated with thermal metal cutting. Here are a few more advantages of using a waterjet cutter.
- No Heat Affected Zones (HAZ) or resin melt
- No fibre pull-out and no mechanical stresses
- Extremely detailed geometry
- Versatility cutting thin or thick materials
- Stack cutting
- Low material loss due to cutting
- Little or no burr
- Scalability – any sized item and any material
- When using a 3D Dynamic Cutting Head, machines can cut chamfers, tapers and intricate geometry which was not possible in the past.
- Dynamic cutting ability automatically compensates for taper and jet-lag in cut parts
Tips For Operating Waterjet Cutting Machines
Waterjet cutting machines are high-pressure devices and can be extremely dangerous. The waterjet stream will instantly slice through clothing, wood, paper, plastics, steel and many other metals which can result in serious injury. Operating any machinery requires extra care and here are some of the most important tips:
- Always operate high power waterjet cutting machines in a clean environment
- No unauthorised personnel should be nearby, including children, pets and spectators (often clients wanting to see how it all works)
- Make sure the work surface is clean
- Always operate the machine on a clean, dry floor without any obstacles
- Never operate a waterjet cutter without wearing proper eye protection
Related: ‘Busting The Myths Of Waterjet Cutters’
Final Thoughts
These machines are extremely versatile, powerful and potentially dangerous, especially when used by an inexperienced or unauthorised person. To ensure top quality fabrication services, PRV Engineering has invested heavily not only in cutting edge machinery but also expertly trained and highly qualified staff. PRV’s state-of-the-art Idroline S1730 hydro-abrasive waterjet cutting system ensures superior technological and productive performance.
If you need quality, professional precision engineering and custom fabrication services, don’t hesitate to contact our team of experts. They will be able to answer any questions you may have and tell you more about our one-stop facility.
For more interesting articles covering all things engineering, manufacturing and technology, follow our weekly blog. You can also join the conversation on Twitter, Facebook, YouTube or LinkedIn using the hashtag, #PRVtech
This site uses Akismet to reduce spam. Learn how your comment data is processed.
Leave a Comments