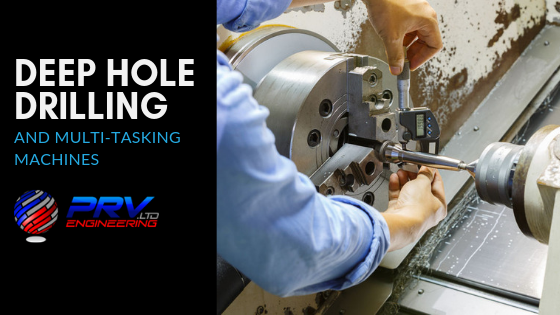
Deep hole drilling, often referred to as gun-drilling, is a highly-specialised machining operation that only a select few engineering companies can perform. This method is used when high-precision round bores are vital to the operation. It produces holes that can be controlled within very tight tolerances, giving much greater accuracy compared to conventional drilling methods.
PRV Engineering is a true one-stop-shop engineering machining service provider offering out of the ordinary services including precision deep hole drilling. Common applications of deep hole drilling include oil and gas exploration, aerospace, armaments and engines. There are essentially three basic types of deep hole drilling categorised as follows:
Gun Drill Method
The cutting tool is a fluted solid rod with a bored hole in the centre where the coolant is injected through a hole in the middle. From there it flows back outside, through the flute and brings the chips with it.
Single Tube System Method
This is only for holes with a diameter of over 15.6 mm as the tubes have a minimum size. Coolant is pumped in around the outside of the cutting tool and pushes the chips out through the centre tube.
Ejector System Method
Ejector Systems are the only acceptable technology for holes over 18.4 mm in diameter. The cutting tool is a tube within another tube where the coolant flows through the smaller one and onto the cutting face. From here the coolant and chips flow back through the larger tube.
Precision Deep Hole Drilling
PRV Engineering is one of a few skilled engineering companies with a deep hole drilling facility in the UK. The service can be supplied as part of an overall manufacturing project or a sub-contracted service. To meet the growing needs of customers, PRV Engineering acquired TEN deep hole drilling machines. The facility also includes all the necessary ancillary equipment to provide a thoroughly comprehensive service.
To ensure that the tightest of tolerances are observed through the deep hole drilling process, PRV also invested in state of the art calibration equipment. With some of the best kit on the market today, PRV Engineering can drill centres of up to 2200mm on non-cylindrical components and 6000mm on cylindrical components.
Multi-Tasking Machining
As the name suggests, these machines can perform multiple tasks and have been around for some time. However, the more obscure the process, the more unlikely it is to be incorporated into this format. Deep hole drilling is an excellent example as it is a highly specialised process.
Deep hole drilling is often required for precision machining components in the oil, gas, and aerospace industries. Putting deep hole drilling into a multi-task format creates an opportunity to offer these industries a higher quality finished product.
Advantages Of Multi-Tasking Machines
The benefits speak volumes as machine breakdowns or scheduled maintenance can result in costly, unproductive downtime. The math is simple; the longer a machine is idle, the less efficient the production process and this is where multi-tasking machines come in very handy.
In addition to actual downtime, you also need to consider moving components around the shop floor. Not only is it labour intensive but you also run the risk of losing or miscounting items within a batch or even misplacing an entire batch. With a multi-tasking machine, all the different operations are done on the same piece of equipment. That means a much smaller chance of downtime and no risk of losing or misplacing any items.
Extreme Accuracy
A vital prerequisite of precision machining success is maintaining extreme accuracy of the holes’ pattern. With deep hole machining (DHM), it becomes challenging to ensure accuracy but that is exactly why it was developed in the first place. Transferring components between machines greatly increase the likelihood of a divergence. However, if the process is handled by one multi-tasking machine, concentricity can be vastly improved.
Conclusion
Deep hole drilling has become more than just making holes as it also gets machined, heat-treated and plated. With that in mind, PRV Engineering offers an extensive range of Gun Drills, Ejector Drills and Counter Boring Heads.
According to Simon Jones, Managing Director at PRV, “We boast years of Deep Hole Drilling experience and have worked closely with a wide range of customers. Our staff are knowledgeable and possess the skills to deliver high levels of accuracy in terms of hole position, diametrical tolerance, surface finish and straightness.”
If you have any questions about deep hole drilling, please leave a comment below or contact us via the website. Maybe you want to share your experience with us on Twitter, Facebook, YouTube or LinkedIn.
This site uses Akismet to reduce spam. Learn how your comment data is processed.
Leave a Comments