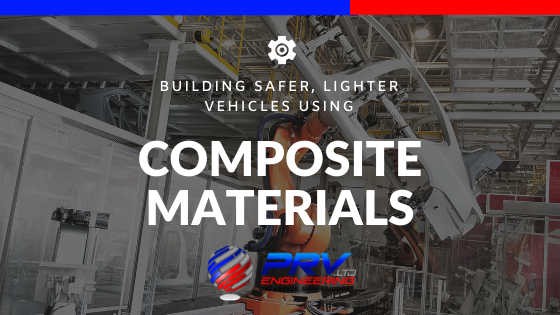
Over the last four decades or so, fibre-reinforced plastics (FRP) have been used in engineering structures. Since then, the use of composite materials has steadily diversified into sports equipment, helicopters, aerospace and high-performance racing cars.
The military first used composite materials before engineering companies applied the technology to commercial planes and cars. It was initially used in military applications such as radomes, secondary structures and internal components. Looking at the automotive future, composite materials can be used to design and build safer, lighter vehicles.
What Are Composite Materials?
Composite materials can be described as using a combination of two or more different materials to produce a material with characteristics from the individual components. Combining the best properties results in a new set of characteristics that the individual materials cannot achieve on their own.
While the individual components remain separate entities, their combined structure sets composite materials apart from mixtures or solid solutions. The new material can be used for different reasons as it could be stronger, lighter or cheaper than traditional ones.
Examples Of Engineered Composite Materials
Composite materials are typically used for buildings, bridges, boat hulls, swimming pool panels, racing car bodies, bathtubs and storage tanks among others. Some of the more advanced examples include applications for demanding environments on spacecraft and aircraft. However, common engineered composite materials include the following:
- Reinforced concrete and masonry
- Composite wood (plywood)
- Reinforced plastics (fibre-reinforced polymer or fibreglass)
- Composite ceramic and metal matrices
- Metal matrix composites and other advanced composite materials
Thermoset composites are formed using glass, carbon, or aramid fibres combined with polyesters, vinyl esters, epoxies or phenolic resins. These particular composite materials are used in several industries but primarily for manufacturing aircraft and aerospace parts.
Research And Development For The Automotive Industry
Thanks to continued research and development within the aerospace industry, composite materials are also being used in transportation. Due to the increasing demand to build lightweight vehicles and components (light-weighting), more engineering companies are using composite materials.
Fibreglass is a popular reinforcing material used in many different applications and a great replacement for steel. As it is extremely durable, companies use fibreglass in vehicle structural components such as drive shafts, bumpers and roof beams.
Reducing the weight of components is vital to increase the efficiency of automotive systems. Considering that carbon fibre has several comparable properties to steel, it weighs considerably less – around one-fifth. Whether it’s a bus, taxi or normal passenger vehicles, reducing the overall weight will result in countless benefits.
Does It Meet The Automotive Industry’s Stringent Demands?
When we compare composite materials directly to steel, they can meet or even exceed the automotive industry’s material property demands. This includes efficient heat conduction, stability for shape retention, corrosion resistance in wet conditions and high-impact strength.
The reduced weight of components made from composites can also help with noise reduction resulting in quieter performance levels. One area in the automotive sector that can benefit greatly from composite components includes electric vehicles.
Using Composite Materials In Electric Vehicles
Even though battery technology is rapidly advancing, it is unlikely that the battery weight will decrease. The primary focus will be on installing more batteries for longer range and more power. This means minimising component weight is crucial and using fibreglass and carbon fibre alternatives would be the ideal solution for electric vehicles.
EV batteries are housed in special boxes to protect them and to prevent passengers from any electrical discharge. Considering that metals are conductive, they aren’t suited for this application which brings us to composite materials. Battery housing made from composites with a higher strength to weight ratio and not conductive will be ideal. Today’s electric vehicles still have a limited range and reducing weight can result in good margins.
Composite Materials In Electronics
Composites are going beyond structural components in vehicles. Several Asian countries are increasing their production of composites as they are becoming increasingly popular in electronics, particularly those who supply the automotive sector.
The global thermoset composites market is expanding due to the increased demand in the automotive and aerospace sectors. As more people want electric and lightweight vehicles, we can anticipate that it will further push the composites market across the globe.
Conclusion
With global governments striving for better energy efficiency standards, reducing vehicle weight is now a more achievable goal. This will greatly aid car manufacturers in meeting these regulations. Composite material development is at a stage now where they are better suited in automotive applications than steel. There is no better time than the present for car manufacturers to consider composites as a truly viable solution.
If you liked reading this article, please follow our blog for more updates in manufacturing, engineering and technology from across the globe. For more information on the products, services and industries that PRV specialise in, please visit the website. You can also join the conversation on Twitter, Facebook, YouTube or LinkedIn using the hashtag #PRVtech.
This site uses Akismet to reduce spam. Learn how your comment data is processed.
Leave a Comments