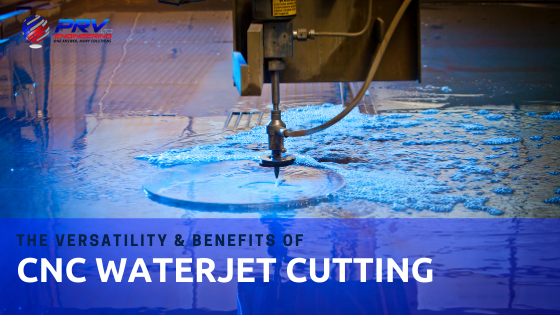
All materials can be cut by the same CNC Waterjet cutting machine, from soft rubber and plastics to the hardest metals and ceramics. This is hugely beneficial for companies who work within several sectors requiring different materials for various applications.
A waterjet cutting machine can ensure identical parts regardless of volumes and produces minimal waste. In this article, discover the many benefits of CNC Waterjet cutting and some of the materials it can cut without a fuss.
CNC Waterjet Cutting Machines
As an introduction, there are water-only cutting and abrasive waterjet cutting. Water-only machines use pure water and can cut soft materials like polymers whilst abrasive waterjet machines use water mixed with an abrasive. This is used when cutting harder materials like aluminium, steel or titanium.
The standard tolerance level for most CNC waterjet cutters ranges from 0.05 to 0.1mm depending on the size. However, tolerance levels can be adjusted to a customer’s requirements and can cut up to 150mm in various sizes. This includes the most intricate projects up to a 4m x 2m profile.
At PRV Engineering, we use hydro-abrasive waterjet cutters to cut virtually any material quickly and with extreme precision. We cut various materials into any shape or size from the most basic mild steels to the more exotic Monel, Inconel, Hastelloy and Titanium.
Materials Suitable for Waterjet Cutting
Due to its versatility and unique characteristics, a CNC waterjet cutting machine can cut all sorts of composites. This includes carbon fibre reinforced plastics, glass-reinforced plastics and almost any metal. The most common application in machine shops is metal, especially aluminium. Below are just some of the materials but it shows just how versatile CNC waterjet cutting is.
Cutting Metals
The Abrasive Water Jet cutting process (AWJ) is a major area of application for waterjet technology involving metal cutting. Here, the process combines finely grained sand with an ultra-high pressure water jet that creates an immensely powerful cutting tool. It can cut metal up to 300mm thick and into any shape. Thanks to the cold cutting process, the cuts are fine and requires very little additional work.
Composite Materials
The word ‘composite’ refers to a wide range of materials all with different qualities and characteristics. This includes Kevlar, carbon fibre, glass fibre, non-woven materials and composite resins among others. To fabricate these materials successfully means using the right cutting process. These are Abrasive Water Jet Cutting (AWJ), Fine Abrasive Water Jet cutting (FAWJ) or Pure Water Jet cutting (PWJ).
Whilst there is an increased demand for composite materials in many industries, very machines can suitably process these materials. The biggest challenge for the other methods is tool wear, something a waterjet cutter doesn’t have to be concerned about. CNC waterjet cutting is widely considered as the best alternative for composite processing thanks to less tool wear and the versatility factor.
Glass Cutting
Using a CNC waterjet cutting machine you can cut glass into any shape without cracking. Glass has been a massive application for waterjet cutting for many years and includes standard glass, composite glass, armoured glass and Plexiglas®.
Glass can easily crack so it requires careful handling and that is where waterjet cutting comes into its own. Waterjet cutting machines can be calibrated and cutting tables adapted to enable low-pressure piercing for smooth handling. Also by using quality abrasives, the risk of chipped cutting edges is minimal.
Cutting Stone and Ceramics
Water jet cutters are used across the world for various small to large-scale stone and ceramic designs. These machines are used in different applications from detailed architectural structures and interior design elements to public art pieces. Thanks to a water jet machine’s free-cutting ability, you can easily transform most stone materials into nearly any shape.
Rubber and Plastics
When cutting rubber, plastics and foam with a CNC waterjet cutting machine, there’s no need for abrasives. For these softer materials, the pure water jet cutting process (PWJ) is the best alternative as it cuts rapidly with narrow cuts of 0.1mm.
With soft materials, water jet cutting presents several benefits to small and large-scale production centres. Instead of punching tools, you can simply use a CNC programme to quickly produce a single part. Also, with a beam, you can mount several parallel cutting heads which enables you to cut large volumes simultaneously.
Cutting Wood Using Waterjets
Waterjet cutting has become the preferred method for processing wood and some specific areas of applications. Today, fabricated wood, such as veneer and plywood are frequently used.
Manufacturers of all types use water jet cutting with some popular applications including wooden jigsaw puzzles, table tennis rackets and wooden furniture. Some of the major benefits of using CNC waterjet cutting on wood include:
- fast setup time
- narrow cuts
- no splintering
- easy free-form cutting
Advantages Of CNC Waterjet Cutting At A Glance
While all cutting processes have certain limitations, CNC waterjet cutting machines are far more versatile. Indeed, it may not be able to cut anything and everything but they can do a lot more than most other machining methods. Here are a few more advantages of using a waterjet cutter.
- No fibre pull-out and no mechanical stresses
- Extremely detailed geometry
- Versatility cutting thin or thick materials
- Stack cutting
- Low material loss due to cutting
- Little to no burr
- Scalability – any sized item and any material
- When using a 3D Dynamic Cutting Head, machines can cut chamfers, tapers and intricate geometry which was not possible in the past.
- Dynamic cutting ability automatically compensates for taper and jet-lag in cut parts
Recommended: ‘8 Waterjet Cutting Myths That Are Total Nonsense‘
Conclusion
Unlike flame, plasma and laser cutting, when using waterjet and abrasive jet machines, there’s no heat during the process. That means these machines can cut various metals, plastics and other materials without melting, distorting or warping them. As a result, the cut paths are smooth and often do not require polishing or any additional fabrication.
To ensure only the best quality fabrication services, PRV Engineering has invested in cutting edge CNC waterjet cutting machines and expertly trained, highly qualified staff. Our state-of-the-art Idroline S1730 hydro-abrasive waterjet cutting system ensures superior technological and productive performance.
If you need help with a manufacturing project, or would simply like more information on our services, get in touch today. You can also follow our blog to stay up to date on all the latest in engineering, manufacturing and technology.
This site uses Akismet to reduce spam. Learn how your comment data is processed.
Leave a Comments