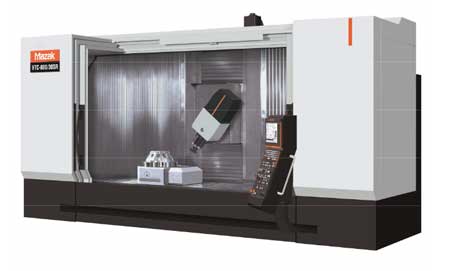
PRV-Engineering is constantly moving with the times and as part of the company’s recent £1.25million investment, managing director Simon Jones has added a vertical travelling column machining centre with full 5-Axis Synchronous milling ability.
Five-sided machining, also known as 3+2, is the process of setting up a part once and using a machine like the Mazak VTC800/30SR to machine five sides instead of machining the part one side at a time using a conventional 3-Axis machining centre.
Simon believes that for most manufacturers investing in any CNC machine tool is a major decision. And though many companies will see 5-Axis as overkill, based on the way they’ve always operated, PRV Engineering believes there are many advantages of having a 5-Axis machining centre. Simon has already seen the fruit of his investment at PRV-Engineering.
“We chose to invest in a state of the art machine and we are delighted with the results. It’s large machining envelope enables us to manufacture a wide variety of components,” said Simon, who with careful consideration to the specific application and the various alternate means of achieving 5-Axis capabilities, believes there are many benefits that five-axis machining can bring.
Simon added; “5-Axis machining is used more often for complex contour work, which may need simultaneous movement of all 5 Axes. Also, recent advances in software have helped make the conversion from three-axis and 3+2 axis positioning to simultaneous five-axis machining accessible to everyday numerical control programmers.
“Some of these techniques might require additional programming time, but the benefits of reduced machining, setup time and reduced hand-polishing outweigh the costs.
Benefits of 5-Axis machining
-
By using a flat bottom end mill and maintaining perpendicularity to the complex surface, machining time can be greatly reduced. This is achieved by stepping over the full diameter of the cutter, which reduces the required number of passes across a surface.
-
5-Axis machining eliminates the multiple set-ups required to re-position the workpiece at complex angles. This saves time and greatly reduces errors and costly tooling and fixture expenses required to hold the workpiece in place.
-
Through the use of shorter tools, five-axis milling can complete an entire part without re-fixturing or using the long tools required in a similar three-axis application and still deliver the final product in less time and with a better surface finish.
-
Over 60% of parts produced in metalworking shops require machining on 5 sides. A more efficient way of manufacturing these parts can make you more competitive, even on less complex jobs.
-
There are less programming costs when you have a 5-Axis machining centre.
-
Providing extra floor space. Companies who have invested in a 5-Axis machining centre can create space by eliminating four or more lathes.
If you want to know more about what the 5-Axis machining centre can produce, why not get in touch or ask your question below? Maybe you are looking for some work undertaken on a 5-Axis centre. If so, why not contact us ?
This site uses Akismet to reduce spam. Learn how your comment data is processed.
Leave a Comments