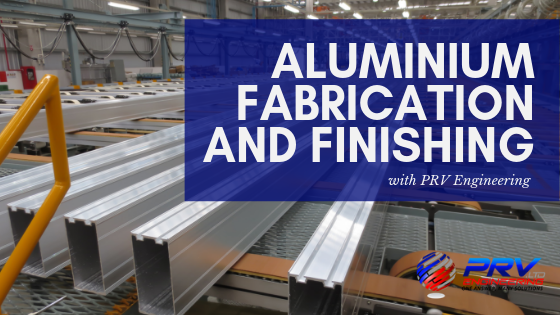
The term “fabrication” means to make something from raw materials whether it’s wood, plastic or certain types of metals. Several industries currently benefit from aluminium fabrication which refers mostly to the construction of metal structures. Choosing a material is a critical decision in all aspects of the production but so is the finishing process.
Although you can fabricate any metal, aluminium is considered one of the most common resulting in big demand for aluminium fabrication services across the world. It’s not surprising if you consider that aluminium is all around us in our homes and office buildings. Some of the most common are aluminium gates and aluminium frameworks used for doors, windows and even showers.
The Aluminium Fabrication Process
Carrying out the aluminium fabrication process requires a variety of specialist tools to join the different pieces together. In the extrusion design stage, optimised extrusions can minimise further fabrication which results in more efficient fitting and assembly. However, even if the extrusion’s properties and functions have been optimised, you often still require some fabrication.
Before starting an aluminium fabrication process, it is important to know the benefits of this particular metal:
- Lightweight and durable
- Malleable and extremely ductile
- Resistant to any form of abrasion and corrosion
- Unaffected by magnetism
- An excellent conductor of heat and electricity
- Flexible to bend into any shape or form
These impressive characteristics, aluminium is more suitable for certain applications compared to other metals. Understanding the properties is essential to maximise your aluminium fabrication process.
Specialist Finishing Processes
When treating the surface of aluminium, it changes the properties which improve corrosion resistance and mechanical wear. In addition, you can also achieve different finishes to enhance the decorative appeal of the final product. We included three of the most common aluminium finishing processes below:
Anodising
Anodising is an electrochemical process often used for protecting aluminium parts that are used to manufacture military machinery and equipment. During this process, the thickness of the naturally occurring oxide layer on the aluminium surface is artificially increased.
Similar to electroplating, the substrate is immersed in an electrolytic bath and connected to an electric current. The aluminium substrate serves as the anode (positively charged electrode), releasing oxygen ions from the bath. The oxygen ions combine with aluminium atoms fully integrated onto the surface of the substrate.
Powder Coating
Powder coating is a popular choice for insulating thick conductors and those with multiple electrical contact points. This provides a protective layer which not only protects against corrosion but also carries great insulation ratings. You can apply powder coating through an electrostatic spray or fluid bath and then cured through a heat-shrink process or UV light.
Profiles are pre-treated to clean and prepare the surface before entering the spray rooms. At this point, the electro-statically charged powder is sprayed onto the surface to form an even coating. Once completed, it goes into a curing oven that melts the powder for an even finish that adheres to the surface. Powder coating is very durable and also offers a virtually unlimited choice of colours. Powder coated surfaces are more resistant to chipping, scratching, fading and wearing than other finishes.
Find out more about Powder Coating, Spray Painting and Shot Blasing at PRV Engineering.
Wet Coating
While you can anodise aluminium or use powder coating for roofing and cladding, the preferred method is wet coating. It’s believed to be a more cost-effective method of coating the material while in coil form. A number of polyester, acrylic and fluorocarbon coatings have been developed and successfully used for decorative and corrosion resistant surface finishes. Service life exceeds 20 years but these finishes do come at a premium price compared to a mill finish.
Related Article: ‘Shot Blasting, Surface Preparation and Specialist Coatings’
Where Is Aluminium Fabrication Mostly Used?
The aforementioned aluminium surface treatments offer slightly different industry applications and here you’ll find a combined list. It includes aluminium applications for anodising, powder coating and wet coating.
- Structural and architectural fabrication of all types – interior and exterior
- Commercial and residential building products including aluminium framework and aluminium gates
- Appliances and furniture, computer hardware, exhibition displays especially in retail
- Food preparation equipment
- Sporting goods and boats
- Components for cars and aircraft
- Industrial piping
- Roofing, cladding and awnings
Although aluminium has good properties, they can actually sometimes make the fabrication process slightly difficult. For that exact reason, it is crucial to find a reputable company capable of providing professional aluminium fabrication services.
Fabrication And Finishing At PRV Engineering
PRV Engineering manufactures products in all materials from the most basic mild steels to the more exotic Monnel, Inconel, Hastelloy and Titanium. Aluminium fabrication is possible using most of the methods and equipment available for other materials. Our state-of-the-art machining centre can undertake fabrication up to 10 tonnes in single weight capacity for various applications.
Whether you need a one-off or a large batch production, PRV can help meet all the requirements from a single source. If you need help with your fabrication project, get in touch with our team of experts always eager to assist. For more interesting stories on engineering, manufacturing and technology, please follow our blog or join the conversation on Twitter, Facebook and LinkedIn.
This site uses Akismet to reduce spam. Learn how your comment data is processed.
Leave a Comments