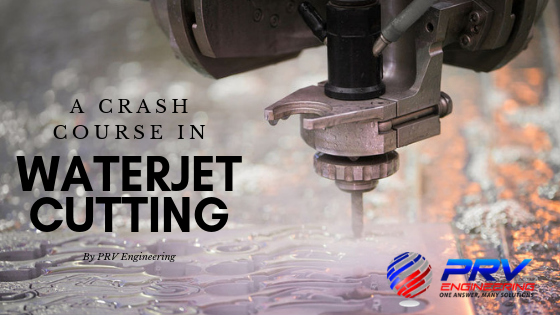
Waterjet cutting is often used during the fabrication process of machine parts. This industrial tool is capable of cutting a wide variety of materials using a very high-pressure jet or stream of water. A mixture of water and an abrasive substance is also used in many applications. The highly versatile cutting method produces much less waste than other forms.
Waterjet cutting is also more environmentally friendly as it doesn’t produce dust, chippings or gas like other cutting methods. Engineering companies are implementing waterjet technology as a cost-effective, complementary machining method to cut parts to near-precise requirements. This greatly helps minimise waste, maximise raw material usage and accelerates overall production.
At PRV Engineering, our advanced equipment allows us to cut and machine all materials from wood, plastic and the very basic mild steels to the more exotic Monnel, Inconnel Hastalloy and Titanium. Let’s take a look at how these machines work and a few of the benefits.
Inside A Waterjet Cutting Machine
Waterjet Cutting allows for more diverse and complex designs with little or no secondary processing required. That is very important at PRV Engineering as we use the Idroline S1730 hydro-abrasive waterjet cutting system. It is just one of many services offered using state of the art CNC Multi-Axis / Multi Discipline machining centres.
Waterjet Machine Components
The basic components of a waterjet cutting machine include the following:
- High pressure pump – generates flow of pressurized water
- Articulated cutting head – computer controlled 5-axis cutting head allows for angled cuts
- Abrasive waterjet nozzle – The ability to cut materials is obtained by pressurising water to extremely high levels and then feeding that water stream through a small orifice. From there it passes through a section where a measured amount of abrasive is added. This mixture results in a coherent stream of abrasive particles traveling at a very high speed.
- X-Y Motion system – accurately moves the nozzle to create the desired cutting path
- Digital CNC communication with remote push-button panel
- Electronic hopper for abrasive automatic monitoring with sensors for cutting parameters and automatic control
- PC Controller – advanced motion controllers are PC based and allows for even inexperienced operators to use effectively
Related Video: Hydro-Abrasive Waterjet Cutting
What Can You Cut Using Waterjet Cutting Technology?
There is a long list of materials that you can cut using this method except for tempered glass. Whatever you’re cutting, remember to factor in the thickness of the material when considering the practicality and cost effectiveness of the project.
A simple example is cutting through 60 cm of foam or rubber compared to 60 cm of concrete. Obviously cutting through rubber, plastic or foam is quick but when cutting metals, the thicker the material, the longer it will take.
Plastic, rubber, wood, glass, metals and composite materials can all be cut using a pure waterjet or hydro abrasive waterjet cutting. Some materials may require adding an abrasive agent to aid effective cutting. Below is an overview of the types of materials that can be cut.
Composite Materials
Heat from other cutting methods can affect composite materials where each element reacts differently. That means that the overall structure of the material can easily be weakened. This does not occur with waterjet cutting as there is no heat affected zone. All sorts of composites such as carbon fibre reinforced plastics, glass reinforced plastics and other composites can be machined.
Rubber And Plastic
As one would expect, soft materials are easy to cut using a water jet and a relatively straightforward process. However, harder or reinforced materials often require adding an abrasive agent to the water jet.
Stone And Concrete
Structural and architectural items can be cut and this includes ceramics, wall panels, counter tops, patterned floor stones and tiles. Thanks to the versatility of waterjet cutting, companies can be more creative when designing wall panels and other items. Architects and designers, for example, can take a more ‘sculptural’ approach with their projects.
Metals
With no heat affected zone in waterjet cutting, the list of metals is long. As mentioned earlier, this includes basic steels, alloys, aluminium, copper and brass to Inconel and Titanium. Polished or reflective surfaces often cause problems for other cutting methods but not when using waterjet cutting machines.
Among other advantages, for the more expensive raw materials, the small kerf and no need to drill ‘pilot’ holes as starting points mean that there is much less material waste which could result in significant cost savings.
How Waterjet Cutting Is Evolving
In the last few decades we’ve seen some significant changes and advancement in abrasive waterjet cutting technologies. For starters, the industry is moving more towards preventive maintenance which was previously a ‘break-fix model’. This means the machine is used until it breaks and then it’s a rush to get it fixed. A major focus has been on making maintenance more accurate and predictable and thus reduce downtime in general.
Evolving Technology
Here are a few ways technology is evolving to help fabricators be more versatile:
- Better software cutting models allow for more accuracy and precision cuts
- Wrist articulation at ±10 degrees (5-axis kinematics with articulated A/B wrist)
- High-precision clamping now allows for faster attachment and removal of cutting heads
- Touchdown height sensor that establishes proper standoff height
- Advanced user interface (UI) in pumps to help operators monitor performance better
- Abrasive recycling systems allow fabricators to capture, recycle and re-purpose used abrasive
Software is also improving the usability experience with a more user-friendly CAD/CAM interface compatible with most file formats. Modern software design is also playing a major role in simplifying the integration of waterjet technology into standard production.
Continued Investment At PRV Engineering
Over the past few years there have been huge investments in equipment and premises. The accuracy and versatility of our waterjet cutting machines ensures that we provide the best possible service. The continuous improvement and investment makes PRV Engineering one of the most progressive engineering companies in the UK.
For more interesting articles on all things engineering, manufacturing and technology, please follow our blog. If you have any questions about PRV Engineering, get in touch through our website or chat with us on Twitter, Facebook and LinkedIn.
This site uses Akismet to reduce spam. Learn how your comment data is processed.
Leave a Comments