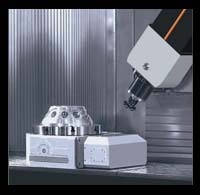
PRV engineering like to move with the times and have invested heavily over the last few years in more modern, improved 5 axis machines. We keep an eye on developments as we want to be able to provide the best service possible.
There are a whole host of reasons why 5 axis machining improves our service. These range from overall time reductions in production to better drilling and programming.
However, technology and development moves on and the latest development is in additive manufacturing. Additive manufacturing (increasingly being known by the more common term 3D printing) is the process of making 3D objects from data by joining successful layers of materials.
Ground breaking developments by German machine tool manufacturer, Hermle have resulted in the ability to integrate additive manufacturing capabilities into a 5 axis machining centre.
The use of energy intensive lasers to melt and fuse successive layers of powder is the standard process when producing additive production 3D metal components. However, Hermle’s metal powder application (MPA) technology process is a thermal spray based on lower energy or kinetic compacting, or microforging.
You might argue that traditional additive manufacturing can achieve similar results to the Hermle MPA method. However theirs moves things on a step further with the ability to micro-forge dissimilar materials, enabling mixed metal solutions like a heat-conducting copper core inside a tool steel exterior.
It has taken more than 7 years and 20 highly qualified engineers to perfect this process at their development centre near Munich, and the firm is now working with German customers to identify suitable applications. They want to find out how the process can be implemented and also how they can produce special dedicated parts.
The current Hermle 5 axis C40U machine is the host platform for the MPA. A powder application nozzle is mounted alongside the vertical milling spindle and a heater is built in to the rotary swivelling table.
To read more detail on the process and what can be produced using it read this article by Engineering.com.
This site uses Akismet to reduce spam. Learn how your comment data is processed.
Leave a Comments