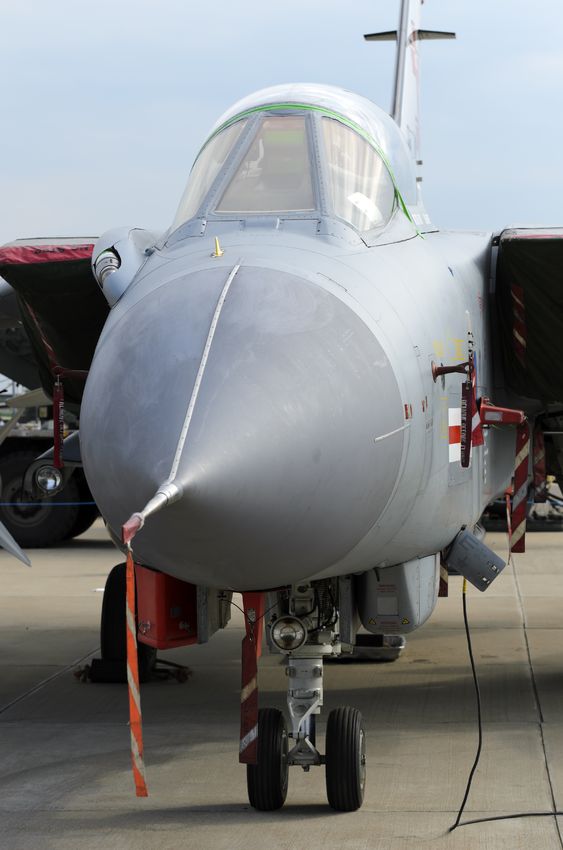
For the past decade, aerospace manufacturers have used additive printing to prototype select parts. For example, the global aerospace industry received a jolt earlier this year when AVIC Heavy Machinery Co. Ltd. of China displayed a 5-meter-long (16.4-foot-long) titanium part fabricated with additive manufacturing, also known as 3-D printing.The process is fast and affordable.
Now, printed aircraft parts have flown for the first time in the UK on board a Tornado jet. Engineers at BAE Systems, who are responsible for the mix of plastic, protective covers and metal support struts, said the components demonstrated how 3-D printing could reduce costs and increase strength compared to conventionally made parts. The latest development is also set to pave the way for their wider use in aerospace.
It’s a fascinating development at a time when BAE Systems has launched a programme of designing and producing 3-D printed components that it claims has cut the cost of repairs, maintenance and service to the Royal Air Force by more than £300,000. The company predicts that over the next four years, the saving will reach a staggering £1.2million.
How does it achieve such savings? Simple. 3-D printing can reduce the cost of producing small numbers of components, because it doesn’t require the creation of custom manufacturing tools. “This will be quite a game changer, not just for the aerospace industry but for a number of industries, producing parts in small batches,” said BAE head of airframe integration Mike Murray in an interview with The Engineer.
“The technology is improving to the point where it could eventually make 3-D printing cost-competitive with some traditional mass-production processes such as injection moulding.”
One of the parts, a plastic cover for a cockpit radio, cost less than £100 to manufacture and cut production time by weeks. A second, a plastic guard for a power take-off shaft, was made as a single part rather than a number of separate components. The engineers also 3-D printed a stainless steel support strut for an air intake door using a Renishaw metal 3-D printer as a demonstration model.
Murray said the 3-D printers had no problem producing components certified for a limited number of flights but more data was needed before they were proven to be of equal quality to traditionally machined parts.
BAE Systems is also undertaking studies with Cranfield and Birmingham universities on producing large frame components to replace conventional titanium frames.
If you have any experience of 3-D printing, let us know. If you have any other engineering queries or requirements, why not look us up at www.prev-engineering.co.uk or on LinkedIn, Twitter and Facebook.
This site uses Akismet to reduce spam. Learn how your comment data is processed.
Leave a Comments