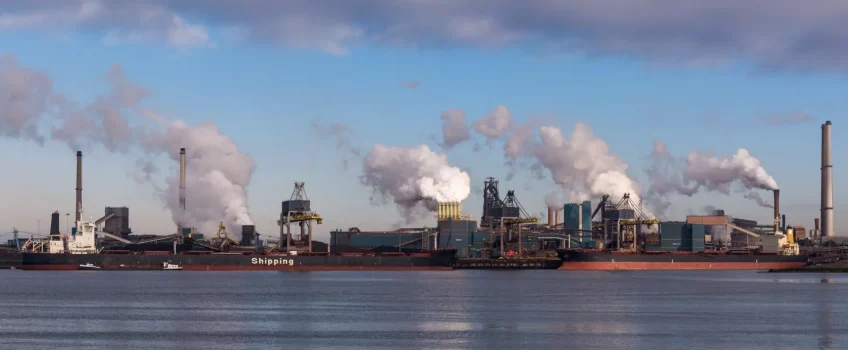
The steel industry is a significant contributor to global carbon emissions, accounting for around 7% of all emissions. As such, decarbonising steel production is crucial for achieving global climate goals and reducing the impact of human activity on the environment. There are several ways to decarbonise the steel industry, including the use of alternative raw materials, such as recycled steel and iron ore, as well as the adoption of new technologies and processes that reduce carbon emissions during the steel-making process. In this article, we explore some of the challenges, benefits and processes of decarbonising steel production.
Barriers To Decarbonising Steel Production
There are several barriers to decarbonising steel production, including the following:
- The high cost and lack of availability of low-carbon technologies and processes, i.e. direct reduced iron and hydrogen-based methods.
- A significant amount of existing infrastructure and equipment is designed for traditional steel-making processes, which can be difficult and costly to retrofit or replace.
- Resistance from some steel manufacturers and industry organisations with concerns about the potential impact on their bottom line and competitiveness
- Regulatory and policy hurdles can make it difficult to implement and incentivise low-carbon steel production at a large scale
Overcoming these barriers will require a concerted effort from governments, industry, and other stakeholders to develop and deploy low-carbon technologies and practices, as well as to create a supportive policy environment.
Finding Alternative Methods Of Steel Production
The process of decarbonising steel production, or reducing carbon emissions produced during the production of steel, is a challenging task. This is because the traditional method of producing steel, known as the “blast furnace-basic oxygen furnace” (BF-BOF) process, is highly reliant on fossil fuels and produces significant amounts of carbon dioxide (CO2) emissions.
One of the major challenges in decarbonising steel production is finding alternative steel production methods that can compete with the BF-BOF process in terms of cost and efficiency. The BF-BOF process has been refined over many years and has a well-established infrastructure, including blast furnaces, basic oxygen furnaces, and supporting industries such as coal mines and coke ovens.
Alternative methods, such as direct reduced iron (DRI) or electric arc furnace (EAF) steelmaking, are still in the development stage and are not yet able to compete with the BF-BOF process in terms of cost and efficiency.
HYBRIT Technology For Producing Fossil-Free Steel
SSAB, a Swedish steel manufacturer along with iron ore producer LKAB and energy company Vattenfall, have come up with an innovative new way to show the world that it is possible to produce fossil-free steel. While the traditional production process emits CO2 as a by-product, the new technology doesn’t have this issue. Instead, the by-product is water!
This HYBRIT technology has the potential to revolutionise our efforts to decarbonise steel production using electric arc furnaces and rolling mills. Here’s how they developed and implemented this technology with a look at future plans. You can read more on the company’s website or click the image below to watch a captivating video on their remarkable achievement.
Decarbonising Steel Production With HYBRIT
The first step toward fossil-free steel production started with the first-of-its-kind direct reduction pilot plant at the SSAB site in Luleå, Sweden which opened in 2020. They continued developing the process of reducing iron ore using fossil-free hydrogen in the pilot plant with the adjoining pilot plant featuring an underground hydrogen storage facility.
- During 2020, the LKAB site in Malmberget produced the world’s first fossil-free iron ore pellets
- They also prepared a demonstration plant in Gällivare, next to LKAB’s iron ore mine with plans to complete construction in 2025
- SSAB’s blast furnace in Oxelösund, Sweden will also be converted into an electric arc furnace at the same time
- Planning to produce iron ore-based, fossil-free steel on a commercial scale in 2026
By the end of 2021, HYBRIT had been granted support from the EU Innovation Fund as one of seven European projects using breakthrough technologies across various industries.
Could Green Hydrogen Help Decarbonise The Steel Industry?
Green hydrogen production involves the use of renewable energy sources, such as wind and solar, to produce clean hydrogen. This process is also known as “green hydrogen” or “renewable hydrogen”.
By using renewable energy sources to power electrolyzers that split water molecules into oxygen and hydrogen, green hydrogen can be produced without emitting any pollutants. The hydrogen produced through this process can then be used in a variety of applications including fuel cells, industrial processes, and transportation.
In addition to being environmentally friendly, green hydrogen is also cost-effective. By using renewable energy sources to produce hydrogen, production costs are significantly reduced compared to traditional methods that require fossil fuels or nuclear power. By investing more in R&D, the steel industry can not only reduce its carbon footprint but also ensure its long-term success.
Also Read: New Carbon Capture Technology Using Hydrogen
The Importance Of Increased Research and Development
Despite its potential benefits, green hydrogen production is still in its infancy. To increase the viability of this energy source, we need a bigger investment in research and development to make the process more efficient and cost-effective.
In addition, governments will need to offer incentives and create regulations to support the growth of green hydrogen production. With the right policies in place, green hydrogen could become a key component in our fight against climate change. By investing in R&D, the steel industry can not only reduce its carbon footprint but also ensure its long-term success.
What Is BioIron And How Can It Help With CO2 Emissions?
The effectiveness of Rio Tinto’s low-carbon iron-making process using ores from its mines in Australia has been proven in a small-scale pilot plant located in Germany. The company is now planning to develop a larger-scale pilot plant to further assess the potential to decarbonise steel production.
The BioIron process uses raw biomass instead of coal to convert Pilbara iron ore into steel while producing little-to-no CO2 emissions. If linked with carbon capture and storage, this process has the potential of becoming net negative emissions.
According to Rio Tinto Chief Commercial Officer, Alf Barrios: “The results from this initial testing phase show great promise and demonstrate that the BioIron process is well suited to Pilbara iron ore fines. BioIron is just one of the pathways we are developing in our decarbonisation work with our customers, universities and industry to reduce carbon emissions right across the steel value chain.”
Conclusion: Decarbonising Steel Production
Decarbonising steel production is an essential part of achieving a carbon-neutral future. The HYBRIT process has shown that it is possible to produce steel without releasing any CO2 into the atmosphere by using electric arc furnaces and rolling mills. Green hydrogen could be a valuable technology to help decarbonise the steel industry further by reducing emissions, improving efficiency and saving energy in production.
With continued innovation, research and development, it is possible that the steel industry can become carbon neutral even quicker than expected. It could also help create jobs while supporting economic growth. By investing in green hydrogen and other technologies to decarbonise steel production, we can put the industry on the path to a greener, more sustainable future.
For more updates on manufacturing, engineering and technology, please read and share our blog or contact us if you need help with a project.