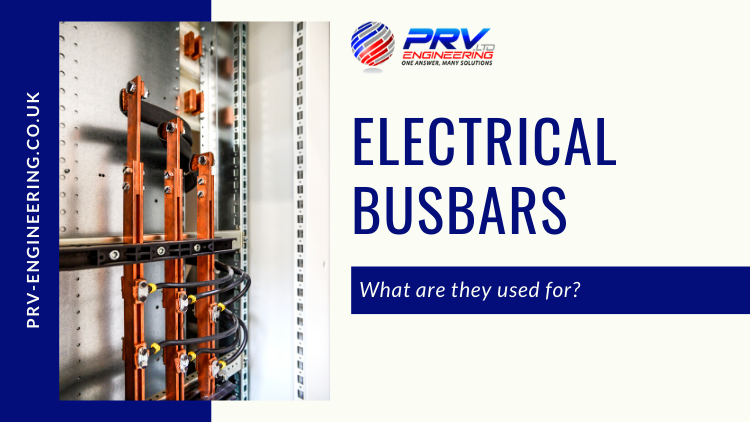
Electrical busbars form the backbone of most power applications and provide the all-important interface between power modules and the outside world. Electrical busbars are a prime example of the latest engineering feats as they make complicated power distribution much easier, cheaper and more flexible.
Even as power applications become smaller, faster and more complex, busbars will remain the primary choice for electrical power distribution. They will also continue to evolve to meet certain requirements and criteria in the future.
In this article, we take a closer look at what electric bussing means, how an electrical busbar system works as well as the benefits and common applications.
What Are Electrical Busbars?
The term busbar, often spelt ‘bus bar’ or ‘buss bar’, is derived from the Latin word ‘omnibus’. It translates into English as “for all” which indicates that busbars carry all of the currents in a particular system.
A busbar is a metallic strip or bar made from copper, brass, or aluminium that ground and conduct electricity. Busbars are usually housed inside switchgear, panel boards and busway enclosures for local high current power distribution. They are also used to connect high voltage equipment at electrical switchyards and low voltage equipment in battery banks.
Electrical busbars are also coated with various materials, such as copper, to provide different conductivity limits and variations. Busbars come in several shapes and sizes which will determine the maximum amount of electric current a conductor can carry before deteriorating (‘ampacity’).
Why Do Bus Bars Need Coating?
Busbars are usually made from corrosion-resistant copper, brass or aluminium in solid or hollow tubes. The shape and size of a busbar, whether its flat strips, solid bars or rods, allow for more efficient heat dissipation due to high surface area to cross-sectional area ratio.
Even though copper oxidises over time, it remains conductive but it this often means more power to push electricity along the surface. Whilst it cannot completely prevent oxidising over long periods, it dramatically reduces the effects.
Coating the bus bar surface will help protect against oxidisation. Busbar coatings typically serve three main purposes:
- To inhibit corrosion
- Increase conductivity
- For cosmetic purposes
As part of PRV’s electrical bus bar manufacturing services, we provide several specialist coatings for additional insulative or conductive properties. We recommended that you read this interesting article covering all the reasons for coating bus bars.
Why Companies Prefer Electrical Busbars
Copper is a popular choice due to the level of resiliency to higher temperatures which offers extra security against short circuits. However, there are many other reasons why companies across various sectors rate busbars so highly, including the following:
- Reduced facility costs and faster installation
- The ability to add, remove or relocate power easily and quickly without any downtime
- Busbars are future-ready and highly flexible as some plug-in units can be disconnected and reconnected without de-energizing
- They require no routine maintenance
- Faster and less costly for expansion or remodelling
- More environmentally friendly as it often requires fewer installation materials and plug-in outlets are reusable and easy to relocate
It’s been proven that changing the shape of an electrical busbar system can greatly improve efficiency due to a bigger, exposed area of the copper surface. This results in a balanced electrical flow while reducing ampacity.
Common Bus Bar Sizes And Applications
Busbars range in size which will depend on the particular use. The most common commercial and industrial busbar sizes are 40 – 60 amps, 100 amps, 225 amps, 250 amps, 400 amps, 800 amps and 1200 amps.
Electrical busbars are also used as housing for expandable track lighting which runs from one single power supply. When space is limited or you need alternative electrical distribution, busbars is the first choice for many industries.
Applications Of Laminated Bus Bars
Laminated busbars has layers of fabricated copper separated by thin dielectric materials. These are laminated into a unified multi-layer composite structure connected to a platoon. Compared to conventional and time-consuming wiring methods, laminated busbars are easy to design and quick to install.
It is known for reliability, low impedance, anti-interference and space-saving. Sizes and applications vary from surface-mounted bus bars the size of a fingertip to multilayer bus bars exceeding 20 feet. They are most commonly used in the following applications and industries:
- High-frequency inverters
- Solar and Wind energy
- Rail applications
- Electric vehicles
- Cellular communication and telephone exchange systems
- Power and hybrid traction
- Power generation systems
- Base stations and Power switch systems
- Military equipment
- Large network equipment
- Power conversion modules
Recommended: ‘Review On Laminated Bus Bars In High-Frequency Inverters’
Applications Of Flexible Bus Bars
Flexible busbars have several thin layers of copper or aluminium designed to efficiently distribute power across an AC or DC system. Copper foils are welded at the mounting areas which makes the ends to rigid for connections whilst the middle remains flexible. Some of the applications include:
- Electric, Hybrid and Fuel Cell vehicles
- Switchgear and transformers in the energy and offshore sector
- Power generator applications in the marine industry
- Transformers and Charging stations
- Switchgear and substations in rail applications, chemical plants and high voltage distribution
- Power link for generators
- Electrical connections in switching cabinets
Leading Suppliers Of Electrical Busbars In The UK
PRV Engineering has been supplying the industry with quality busbars, conductors, contacts and connectors for many years. We specialise in the use of copper to manufacture all components for low, medium and high voltage industries. This includes rail rolling stock and trackside electrical components.
PRV understands and can meet your needs whether you’re an International manufacturer of medium or high voltage distribution and transit switchgear, or an independent engineering contractor specialising in low voltage, high voltage and extra-high voltage electrical plants and equipment.
Some of the services we offer clients in the electrical industry include:
- Punching and folding
- Forging and pressing
- Complete machined castings and stampings
- Busbar fabrication
- Plating and heat shrink sleeving
If you have a project in mind or need more information on our electrical busbars, get in touch today. You can also follow our blogs and join us on social media using the hashtag #PRVtech.