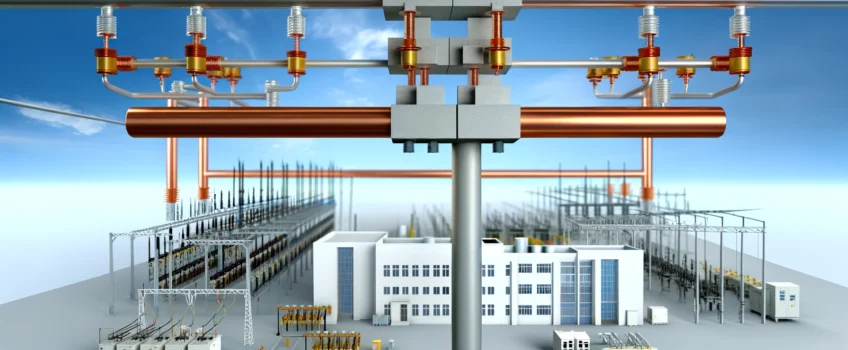
Busbars are an integral part of most electrical systems, yet many people may not be familiar with their purpose or how they are made. In this guide, we will explore the basics of busbar manufacturing and why it is essential to choose a reliable bus bar manufacturer for your specific needs.
What Are Busbars?
Busbars, essential components in the electrical power distribution field, serve as critical conduits for conducting electricity within a wide array of electrical systems. These metallic strips or bars, predominantly made from copper or aluminium, ensure the efficient and safe distribution of electrical power. The inherent properties of these metals, including excellent conductivity and resistance to corrosion, make them ideal for busbar fabrication. The process of busbar manufacturing involves cutting, bending, and drilling these metals into specific shapes and sizes to meet the precise requirements of various applications.
The versatility of busbars extends beyond mere electrical conductivity. Their design significantly reduces the space required for cable installations and enhances the overall efficiency of power distribution systems. Busbars are not only fundamental in distributing power across electrical switchboards, distribution boards, and substations but also play a pivotal role in renewable energy systems and battery banks, underscoring their importance across diverse sectors.
The Busbar Fabrication Process
Busbar fabrication, a cornerstone in the realm of electrical engineering, entails a meticulous process that transforms raw metals into precision-engineered components. This process begins with the selection of high-quality copper or aluminium, followed by cutting these metals into strips or bars. The subsequent steps involve punching, bending, and drilling to achieve the desired shape and configuration, ensuring that each busbar meets the specific requirements of its intended application.
Advanced manufacturing techniques, including CNC machining and laser cutting, contribute to the precision and efficiency of busbar fabrication. These methods allow for the production of busbars with exact dimensions and tolerances, facilitating their integration into complex electrical systems. The fabrication process also encompasses the application of protective coatings and insulation to enhance the durability and performance of busbars in challenging environments.
Common Uses of Busbars
Busbars play an indispensable role in the distribution and management of electrical power across various sectors. In industrial settings, they are crucial for distributing power to heavy machinery and equipment, ensuring a stable and reliable power supply. In the renewable energy sector, busbars facilitate the efficient transmission of power from solar panels and wind turbines to storage units and the grid, highlighting their significance in sustainable energy systems.
Moreover, busbars are integral to the infrastructure of electric vehicles (EVs), where they connect batteries to motors, delivering the power needed for propulsion. This application underscores the growing importance of busbars in supporting the transition towards cleaner transportation options. The flexibility and efficiency of busbars make them a preferred choice for power distribution in data centres, telecommunications, and high-rise buildings, further demonstrating their widespread utility.
Coating Busbars for Specific Industries
The process of coating busbars is a critical aspect of busbar manufacturing, especially for applications in harsh or demanding environments. Coatings, such as tin plating and silver plating, are applied to busbars to enhance their conductivity, corrosion resistance, and overall longevity. Tin plating is commonly used for its excellent corrosion resistance and solderability, making it suitable for a wide range of applications, including in the automotive and renewable energy sectors.
Silver plating, on the other hand, offers superior electrical conductivity, making it the preferred choice for high-frequency applications or environments where minimal electrical resistance is paramount. The selection of the appropriate coating depends on the specific requirements of the application, including the operating environment, electrical load, and durability expectations.
Related: Which Is Better, Silver Plating Or Tin Plating for Busbars?
Looking for a Truster Busbar Manufacturer In The UK?
At PRV Engineering, we pride ourselves on delivering expert, quality, reliable, and affordable engineering and fabrication solutions. With over 30 years of experience, our busbar production lines and professional staff are adept at managing both large and small production batches, ensuring competitive prices without compromising on quality.
For businesses in need of industrial busbar fabrication, PRV Engineering offers a comprehensive service, from punching and folding to plating and heat shrink sleeving. Our dedication to using copper for all components in low, medium, and high voltage industries, including rail rolling stock and trackside electrical components, underscores our commitment to quality and reliability.
To learn more about our busbar fabrication services or to discuss your engineering or custom fabrication project, get in touch today. Follow our blog and join the conversation on social media for the latest developments in engineering, manufacturing, and technology.