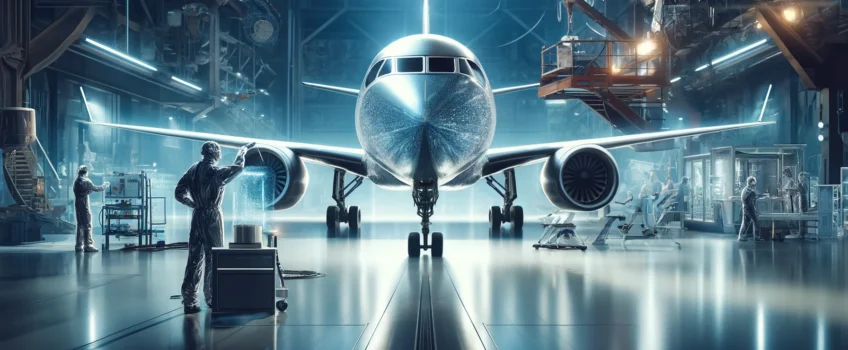
Considering the precision required in aerospace design, integrating cutting-edge materials and protective coatings for aircraft stands as a pillar in advancing modern designs. These technologies not only enhance aircraft performance and safety but also contribute significantly to the sustainability goals of the industry. In this article, you will gain a better understanding of the significant role of protective coatings for aircraft manufacturing, offering insights into their benefits and applications.
The Role of Powder Coating in Aircraft Durability
Aerospace powder coating is a superior finish used on various aircraft parts, from the fuselage to the tiniest components like fasteners. The primary reason for its extensive use in the aerospace industry is its ability to provide a durable, corrosion-resistant coating that withstands the harsh conditions of aviation environments. This type of coating not only extends the life of aircraft parts but also significantly reduces maintenance time and costs.
- Enhanced Protection: Aerospace powder coatings protect critical components against environmental factors such as UV radiation, moisture, and extreme temperatures.
- Weight Reduction: Unlike traditional liquid paints, powder coatings are lighter, contributing to the overall reduction in aircraft weight, which is crucial for fuel efficiency and environmental sustainability.
Recommended: Introduction to Precision Engineering in Aerospace Manufacturing
Innovative Protective Coatings for Aircraft Efficiency
Protective coatings for aircraft are not limited to exterior paint. They encompass a range of applications including thermal barriers in engine turbines and anti-erosion layers on leading edges of wings. These coatings are tailored to meet specific performance criteria, ensuring that every aircraft part optimally contributes to the overall efficiency and safety of the aircraft.
- Thermal Coating Applications: High-performance coatings in engine turbines help manage extreme heat and reduce thermal fatigue, thereby extending engine life.
- Hydrophobic Coatings: Applied on aircraft exteriors, these coatings help reduce drag by minimising moisture accumulation on the aircraft’s surface during flights. This translates to increased fuel efficiency and reduced emissions.
- Anti-Corrosion Coatings: Applied on metal parts, these coatings provide a protective barrier against corrosion, preventing costly maintenance and repairs.
Precision Engineering and Its Role in Aerospace Manufacturing
Precision engineering is critical in aerospace manufacturing, where every micron matters. The production of turbine blades, a prime example, showcases the high level of accuracy required. These blades must endure extreme temperatures and pressures, and even the slightest deviation can lead to disastrous consequences.
- Safety and Reliability: With precision engineering, components such as landing gear and turbine blades achieve a high level of reliability and safety, crucial for effective aircraft operation.
- Cost Efficiency: Through precise manufacturing processes, companies can avoid costly downtimes and maintenance, ensuring long-term operational savings.
What Are The Different Types of Protective Coatings for Aircraft?
Understanding the different types of protective coatings used in aircraft can help industry professionals make informed decisions about their specific applications. For example, while powder coating is ideal for large surface areas, other coatings like thermal barrier coatings may be better suited for engine components.
- Epoxy and Polyurethane Coatings: Common for aircraft exteriors, offering robust protection against chemical and UV damage.
- Ceramic Coatings: Used in engines for heat resistance and in cabins for aesthetic and functional purposes.
- Specialised Coatings: Such as those for electromagnetic interference shielding or radar-absorbing materials used in military applications.
- Fluoropolymer Coatings: Highly resistant to corrosion and abrasion, fluoropolymer coatings are used on aircraft parts exposed to harsh environments such as saltwater and chemicals.
Protective Coatings for Aircraft: Embracing The Future of Design
As the aerospace industry continues to evolve, so do the demands for innovative protective coatings. With new technologies emerging, such as self-healing and anti-icing coatings, the future of aircraft design is constantly pushing boundaries. These advancements not only improve performance and safety but also contribute to the overall sustainability of the industry.
- Self-healing Coatings: Utilising microcapsules filled with a healing agent, these coatings can repair small damages before they become critical.
- Anti-icing Coatings: Applied on aircraft surfaces, these coatings prevent ice buildup, reducing the risk of accidents and improving fuel efficiency.
What Does PRV Engineering Have To Say?
As the aerospace industry continues to evolve, the integration of advanced materials and protective coatings will play a crucial role in shaping the future of aircraft design. By embracing these technologies, the industry not only enhances the performance and safety of aircraft but also steps forward in its commitment to environmental sustainability.
As a leading precision engineering company, PRV Engineering is at the forefront of these advancements, providing high-quality coatings and services for the aerospace industry, defence, automotive and busbars, among others. With our expertise in precision engineering and our commitment to innovation, we are proud to be a part of the exciting future of protective coatings for aircraft. For more insights into aircraft design of the future, please follow our blog and read this informative article.