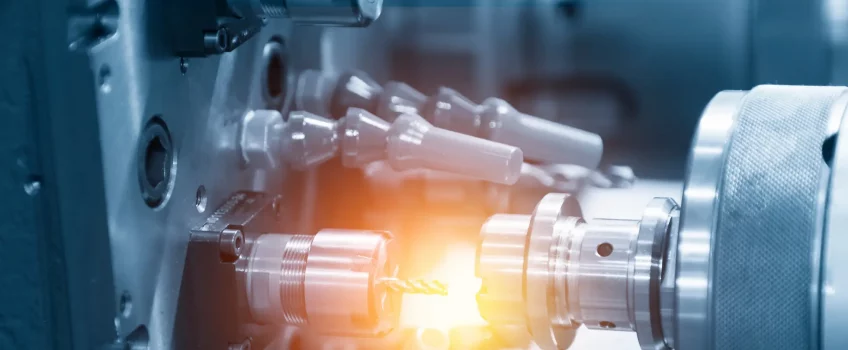
Precision engineering is a crucial aspect of modern manufacturing, allowing for the creation of complex products with high levels of accuracy and reliability. The importance of precision engineering cannot be overstated, especially in industries such as aerospace and medical technology. In this article, we will explore the process of moving from blueprint to reality, highlighting the key role that precision engineering plays in this process.
What is Precision Engineering?
Precision engineering is the process of designing and producing parts or components to extremely tight tolerances. This involves the use of advanced technology and specialised equipment to achieve a high degree of accuracy in the manufacturing process. Precision engineering is essential in just about every industry but especially in the following sectors where the components must be produced to exacting standards:
- aerospace
- automotive
- medical
- electronics
- defence
From Blueprint to Reality: The Precision Engineering Process
The process of moving from blueprint to reality involves several stages, including design, prototyping, testing, and production. It plays a critical role in each of these stages, ensuring that the final product meets the required specifications. Let’s start at the beginning with design.
Design
Design in precision engineering involves the creation of precise and detailed plans for the development and production of certain components, products, and systems that meet specific requirements and design standards. This process typically involves using computer-aided design (CAD) software and other specialised tools and techniques to create 3D models and technical drawings that accurately represent the intended design.
The design phase also includes choosing the most appropriate materials, manufacturing methods, and quality control measures to ensure that the final product meets the required specifications and performs as it should. This is a crucial step in the manufacturing process as it lays the foundation for the entire production process and directly impacts the quality and performance of the final product.
Prototyping
Once the design is finalised, the next step is to create a prototype. This involves creating a preliminary physical model or sample of a product or component to test its design and functionality before putting it into full-scale production.
It typically also involves using computer-aided design (CAD) software and specialised equipment such as 3D printers, CNC machines, and laser cutters. The prototype can be used to test the design and identify any issues that need to be addressed before moving on to production.
Testing
Before the component can be approved for production, it must undergo rigorous testing to ensure that it meets the required specifications. This involves using a range of advanced testing equipment to assess the component’s performance and durability. The precision engineering team will work closely with the testing team to analyse the results and make any necessary adjustments.
Production
Once the component has passed the testing phase, it can move into production where the engineering team will use their expertise and specialised equipment to produce the component to the required tolerances. The process often involves a range of steps — from material selection to cutting and shaping, finishing, assembly, and quality control (QC).
Since the smallest deviations from the intended design specs can result in significant quality issues, precision engineering production requires a high level of accuracy and attention to detail. As such, many precision engineering companies use advanced machinery and automated assembly systems while performing quality checks throughout the production process.
The Benefits of Precision Engineering
Precision engineering offers a range of benefits, including improved product quality, increased efficiency, and reduced costs. By using advanced technology and specialised equipment, precision engineering can significantly reduce the time and cost required to produce components. This allows for faster production times and reduced lead times, improving the overall efficiency of the manufacturing process. Other benefits include the following:
- Produce high-quality components with a high level of accuracy and reliability
- Allows for the creation of complex shapes and features, which would be impossible to produce using traditional manufacturing methods
- Ensures that the components are produced to exacting standards, reducing the risk of defects or failures
- Precision engineering can help to reduce the risk of defects and failures which leads to increased customer satisfaction and improved brand reputation
The Importance of Choosing the Right Engineering Partner
Choosing the right engineering company is crucial for the success of any project. They will have the expertise and experience required to produce components to the required specifications, while also providing excellent customer service and support throughout the process.
When looking for a reputable precision engineering partner, it is important to consider factors such as their experience, expertise, and reputation in the industry. You should also check their ability to provide customised solutions that meet the specific requirements of the project.
Recommended: How The Right Engineering Company Can Benefit You
Is Precision Engineering A Good Career?
Yes, precision engineering is a great career choice for those who are detail-oriented and obsessed with high quality. Precision engineers are in high demand due to their advanced technological knowledge and ability to work with complex products. They also benefit from a good salary and job security. However, it’s important to remember that becoming a precision engineer requires dedication, hard work, and a willingness to learn.
How Do I Become A Precision Engineer?
If you’re interested in becoming a precision engineer, the first step is to get a bachelor’s degree in mechanical engineering or a related field. You should also look into gaining some experience in engineering or manufacturing by completing an apprenticeship programme at a local precision engineering company and gaining additional certifications such as CNC programming. This will help you develop your skills and knowledge as you expand your career.
Conclusion
Precision engineering is a critical aspect of modern manufacturing, allowing for the creation of complex products with a high level of accuracy and reliability. From design to production, the process requires specialist equipment, highly-skilled personnel, and comprehensive testing procedures to ensure the components meet the required standards.
Consequently, choosing the right engineering partner is essential for achieving success in any project. By working with an experienced precision engineering company, businesses can benefit from improved product quality, increased efficiency, and reduced costs. This ensures successful outcomes for projects, as well as increased customer satisfaction and a strong brand reputation.
Why Choose PRV Engineering?
PRV Engineering is a reliable and reputable engineering company with over 35 years of industry experience. Their expansion and development of a well-equipped facility in Pontypool, South Wales, along with their skillsets including CNC machining, Deep Hole Drilling, Welding and Fabrication, CAD/CAM links and Mechanical Installation Teams, allow them to offer a diverse range of services and products for clients across various sectors.
With a strong focus on quality, all products and services are provided in accordance with their Quality Standard BS EN ISO 9001:2008 certification, ensuring that clients can trust in the reliability and precision of their work. If you require machining components, steelwork fabrication, installation or maintenance, PRV Engineering should be your first call for one-off or large batch production.