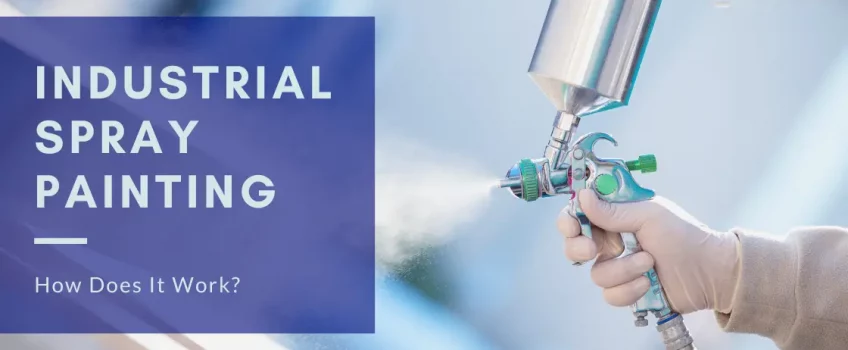
Industrial spray painting may not involve creating works of art but it still requires a high level of skill to perform the job well. Industrial spray painting works with several types of liquid materials including certain paints, stains and primers. Among the greatest benefits of commercial spray painting is the high degree of control and even finish on all types of surfaces.
Why Does Heavy Machinery Need Industrial Spray Painting?
Many customers contact PRV Engineering for industrial or commercial spray painting of heavy machinery but what is the purpose? Well, the main reason is to ensure that their machines don’t rust and to keep the machines looking good with no old paint chips potentially contaminating the products they are producing.
Industrial spray painting techniques are custom designed to protect the material underneath the equipment to prevent natural wear and tear. The type of coatings may vary depending on the type of equipment and material but some of the most popular coatings include Epoxy, Urethane and Line X paints.
How Is Industrial Spray Painting Done?
Whether your equipment is made from steel or sandblasted, the surface must be free from rust, debris or stains otherwise the paint will not bind to the surface properly and it will peel off prematurely.
- The process usually starts with a high-pressure wash using specialist equipment which will clean the surface and prepare it for painting
- The next stage is to apply a primer which will help the paint to adhere to the surface and create a smooth finish.
- Once the primer has been applied, the industrial spray painting can begin.
- The final stage is to apply a top coat which will provide additional protection against the elements and further reduce the risk of rusting
Important Considerations Of Industrial Spray Painting
Painters use various techniques in conjunction with a variety of sprayers and other technology to apply paint to machinery. However, the main variables that industrial spray painters MUST consider when performing any industrial spray painting job are as follows:
Substrate Preparation
When we talk about the substrate, it’s the preparation of the surface that requires painting. As mentioned in the previous section, painters have to ensure that the substrate is cleaned properly for an even and proper finish as almost 80% of jobs fail due to improper surface preparation.
Paint Thinning
There are times in the painting process when the paint needs to be thinned out for proper application and coverage. Thinners are different from each other on the basis of what they can dissolve, their odour and flammability. For most paints, mineral spirits, along with an alkyd or oil base, can be used for thinning paint but other paints may require different thinners.
Spraying
The actual spraying also requires great care and precision. Variables in the industrial spraying process include the required type of finish, the type of paint being used and the substrate type.
There’s a large variety of spraying devices and guns that can be used, so industrial painters must consider all the variables and choose the right spray painting device to achieve the desired results. Painters also have the flexibility to choose the amount of pressure that the paint is applied with and this is measured in pounds per square inch.
Commercial Spray Painting Methods
There are several types of spray painting methods, each with its own pros and cons. Many companies use an airless sprayer for greater control over the paint finish. It also helps to reduce wastage since the machine recirculates any excess paint. Below is a breakdown of a few industrial spray painting methods.
Air Gun Spraying
The spray gun, which originated from the airbrush, is commonly used for more delicate work such as coating lacquers, paints, varnishes, shellac, and other finishes. Air spraying applies the paint using a spray gun or sprayer through air and fluid compression which is known as atomisation.
Electrostatic Spray Painting
Electrostatic air spraying is a modern technique that is used extensively in the automotive sector. It provides an even coverage on surfaces such as metals, doors, windows, railings, and metal fencing. This painting method requires specialised equipment such as air-assist guns and HVLP (High Volume, Low Pressure) sprayers.
HVLP (High Volume Low Pressure)
Similar to the electrostatic air or airless spraying technique, HVLP relies on turbines and heat, which stabilises the paint and reduces atmospheric condensation for enhanced adhesion. Here, the paint is propelled out at high volumes and uses low airflow pressure to reduce spraying waste. The air pressure at the air cap must be 0.1-10 PSI or show that the application is at least 65% transfer-efficient.
LVLP (Low Volume Low-Pressure)
Low Volume Low-pressure industrial spray painting means it uses less air volume and lower air pressure compared to a typical HVLP process. LVLP spray painting guns are not limited to 10 PSI at the air cap but can still be compliant by delivering 65% or better transfer efficiency.
Airless Spray Guns
The airless spraying technique simply involves pushing the paint through a hose connected to an attached nozzle, instead of relying on compression as with some of the previously discussed methods. The viscosity and surface tension keeps liquid films intact, while the nozzle flow distributes paint mists uniformly. The airless spray gun method is best suited for glossy, glass-smooth textured coatings.
How Does Industrial Spray Painting Differ From Other Types Of Painting?
The type of painting you would do at home is widely different as industrial spray painting involves many different variables that must be considered. Industrial painters, for example, must determine whether the paint is flammable and how well it will perform and its longevity under extreme temperatures which is likely to get very high during operation.
Powder Coating And Spray Painting At PRV Engineering
To meet the increasing customer demand, we are continuously investing in staff training and sourcing high-quality machinery. Our finishing department comprises of a 6-metre Shot Blast room, various Shot Blast cabinets, Powder Coating booth, Wet Paint spray room and a 2.2-metre cubic High Bake Oven.
We have the knowledge and means to provide customers with a high-quality painted finish to very exacting standards. And, as part of our Busbar manufacturing services, we offer various specialist coatings to provide additional insulative or conductive properties using an electrostatic spray, fluid bath or simple heat shrink processes.
We can also test the finishes for the following:
- Gloss level
- Coating thickness
- Adhesion strengths
- Porosity
- Colour shade
- Dielectric strength
- Insulative or conductive properties
If you are interested in talking to us about your industrial spray painting requirements, contact PRV Engineering today or read our blog for more interesting articles on engineering, manufacturing and technology.