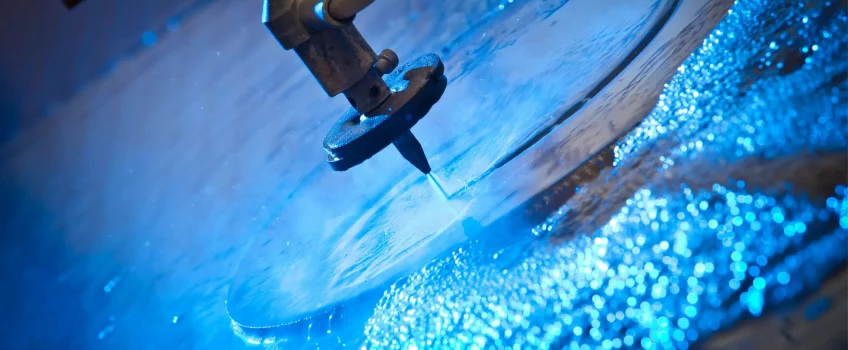
How Hydro-Abrasive Waterjet Cutting Compares to Traditional Methods
Hydro-abrasive waterjet cutting is a precision cutting technique that uses a high-pressure stream of water mixed with an abrasive substance to cut through materials. It is a versatile process that can be used to cut a wide range of materials, including metals, composites, glass, stone, and ceramics. In this article, we explore the advantages of this advanced process and some of its applications across various sectors.
5 Benefits Of Hydro-Abrasive Waterjet Cutting
Hydro-abrasive waterjet cutting is a powerful and versatile tool that offers a number of benefits over traditional cutting methods. It is an increasingly popular choice for businesses in a variety of industries, and its capabilities continue to expand as technology evolves. Some of the key benefits of hydro-abrasive waterjet cutting include:
1. Heat-free cutting
One of the main advantages of hydro-abrasive waterjet cutting is that it can cut materials without generating heat. This is important for cutting sensitive materials that may be damaged by heat, such as certain plastics and composites. It also allows for a cleaner cut, as there is no heat-affected zone (HAZ) on the material being cut.
2. High precision
The waterjet stream can be focused to a very small diameter, allowing for intricate cuts and shapes to be made with a high level of accuracy. This makes it ideal for applications where precise cuts are required, such as in the aerospace or medical industries.
3. Versatility
Hydro-abrasive waterjet cutting can be used to cut a wide range of materials, including metals, composites, glass, stone, and ceramics. This makes it a versatile tool for businesses in a variety of industries.
4. Environmental friendliness
Hydro-abrasive waterjet cutting generates very little waste, as the abrasive substance is recycled and the water used in the process is captured and reused. This makes it a sustainable choice for businesses looking to minimize their environmental impact.
5. Reduced material waste
Because hydro-abrasive waterjet cutting is a highly precise process, it can help reduce material waste by allowing for more efficient use of raw materials. This can help reduce costs and improve the bottom line for businesses.
What Are The Disadvantages Of Hydro-Abrasive Waterjet Cutting?
However, hydro-abrasive waterjet cutting can be slower and more expensive than other cutting methods, and it is not suitable for materials that are thicker than a few inches. It is also not suitable for materials that are highly reflective or have a hard, brittle surface, as the abrasive particles can cause chipping or cracking.
What Is Hydro-Abrasive Waterjet Cutting Used For?
Hydro-abrasive waterjet cutting machines use a high-pressure stream of water mixed with abrasive particles to cut through just about any material. It has a wide range of applications in a variety of industries, including the following:
Custom Fabrication In Aerospace and Defence
With the ability to cut metals without any heat exposure, water jet cutting has become a popular option in industries such as aerospace and defence. This cutting technique can be applied to a wide variety of materials – from Kevlar composites used for personal or vehicle protection to thick plate steel measuring 250mm, for example. In the aerospace sector, these machines can create small vanes and blanking titanium plates to produce fan blades.
With no heat-affected zone (HAZ), components are left relatively stress-free compared to traditional metal-cutting methods. Many fabricators should be able to use special markings to display important information for traceability and sourcing purposes, including part numbers, material batch numbers and order numbers.
Cutting A Variety Of Special Metals
Hydro-abrasive waterjet cutting machines can cut a wide selection of metals from a thickness of 1mm to 300mm. Some of these materials include the most basic mild steels and titanium to monel, inconel, hastelloy and titanium. By harnessing the power of water jet cutting, you can drastically reduce your overhead expenses and completion time, allowing for quick production of machine parts with tight tolerances that don’t require finishing in a separate process.
General Sheet Metal Cutting And Fabrication
Abrasive waterjet cutting is the optimal option for lower batch sizes and custom designs due to its precision and versatility. Whether it be large production runs or one-off bespoke designs, this process can easily accommodate projects that require working on stainless steel, carbon steel, yellow metals and aluminium in a short period of time.
Many waterjet cutting machines are particularly suited to the fabrication industry as they can perform multiple functions in the same process. For example, some can produce countersunk holes in the same operation as the main profile which can help eliminate positioning errors that are common with secondary operations. The machine’s ability to produce a diversity of weld preparations with unparalleled accuracy meets the rigorous demands for secure welds.
Recommended: Custom Fabrication, Welding and Finishing
Cutting Stone, Ceramic and Glass
Hydro-abrasive waterjet cutters are a fantastic option for cutting an array of materials with precision and accuracy. Whether you require thin ceramic tiles or thick granite adorned with stainless steel, brass, copper, or stone inlays – you can cut it all on the same machine.
Specialised software modules let you scan and combine original artwork for maximum material utilization. For paving and tiling projects, the grout width is taken into consideration to ensure a smooth, natural appearance. With this advanced technology, each pattern will blend seamlessly with its surroundings!
Also Read: How Does Waterjet Cutting Work?
Hydro-Abrasive Waterjet Cutting In The Medical Sector
Hydro-abrasive waterjet cutting is becoming increasingly popular for use in the medical sector as it can cut through materials with absolute precision and minimal waste. It can be used for a wide range of applications, from surgical implements and medical devices to complete prosthetics.
The stream of water used in hydro-abrasive cutting is highly accurate and can achieve tolerances as low as 0.003″ with no heat distortion or mechanical deformation. As a result, it is possible to fabricate parts from sensitive materials such as titanium and stainless steel that would not be suitable for other cutting processes.
Since it is also relatively non-invasive, it reduces the risk of contamination and allows for repeatable cuts over time. It is possible to produce 3D parts with multiple levels of complexity, such as internal channels or holes, with no additional post-processing work required.
What Abrasives Do They Use In Waterjet Cutting?
There are a variety of abrasive particles used for waterjet cutting, such as silicon carbide, aluminium oxide, sand and garnet. Of these options, garnet is the most common due to its physical properties. It is hard and dense enough to cut through a wide range of metals, yet still soft enough to avoid leaving burrs on the finished product.
The size of the grit depends on the material being cut. For example, finer particles are better suited for softer materials while coarser ones work best on metals with higher tensile strength. The choice of abrasive also affects the speed and quality of the cut, so it’s important to select the right combination for your application.
How To Choose The Right Pressure In Abrasive Waterjet Cutting
The pressure of the stream of water used in abrasive waterjet cutting is one of the most important factors that will determine the speed and quality of your cuts. In general, a higher pressure will result in faster cutting speeds, but it also increases wear on your nozzle. Furthermore, certain grades of abrasives may be better suited for higher or lower pressures.
To ensure that your waterjet cutting process is as efficient and accurate as possible, it’s essential to select the right combination of abrasive and water pressure. By taking these factors into account, you are almost guaranteed that your waterjet cutting machine will provide an optimal finish regardless of the material being cut!
Conclusion: Hydro-Abrasive Waterjet Cutting
The process offers a range of advantages over other methods and as such is quickly becoming the preferred method for medical device fabrication. As technology advances, it is likely that its popularity in this sector will only continue to grow. Furthermore, compared to other machining processes such as laser cutting, it is much more cost-effective.
Hydro-abrasive waterjet cutters have been proven to be the ideal solution for intricate shapes and designs. Not only are they precise, but their powerful jets also make quick work of tough materials like hardened steel or tungsten. This technique is also perfect for creating complex curves and other forms with accurate results every time!
At PRV Engineering, our state-of-the-art Idroline S1730 hydro-abrasive waterjet cutting system ensures superior technological and productive performance. Contact our team of experts if you need help with a project or if you have any questions about waterjet cutting.