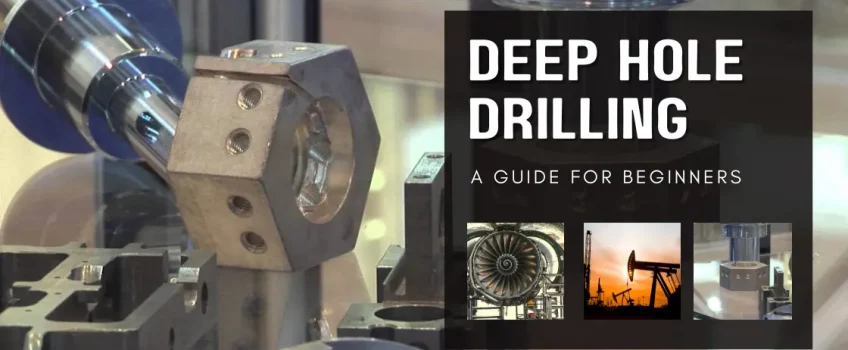
Deep hole drilling is a machining process that can produce holes up to ten times deeper than the diameter of the hole and is suitable for a variety of metals, including the strongest of superalloys. Deep hole drilling services require special tools and setups to deliver high-pressure coolant, cleanly evacuate chips and reach the depth-to-diameter. Deep hole drilling, also known as gun drilling, is a highly-specialised machining operation that only a few engineering companies can perform, including PRV Engineering. Here is a closer look at some of the processes, applications and pros and cons.
Deep Hole Drilling Services: Precision Honing, Trepanning, Gun Drilling and BTA Drilling
The honing operation is an abrasive machining process that produces a precision surface on a metal workpiece by using a special tool. This honing tool is composed of abrasive grains that are held together in a binder. The abrasive grains are constantly renewed as they wear down during the honing process.
Gun Drilling
Gun drilling is a machining process that produces a deep, narrow hole in a workpiece. The hole is produced by using a rotating drill bit with cutting teeth. Gun drilling is performed using a gun drilling machine, which consists of a spindle, a chuck, and a coolant system.
BTA Drilling Services
BTA drilling is a machining process that produces a deep, narrow hole in a workpiece. The hole is produced by using a rotating drill bit with cutting teeth. BTA drilling is performed using a BTA drilling machine, which consists of a spindle, a chuck, and a coolant system.
What Is Trepanning?
Trepanning, pronounced TREE-panning or treh-PAN-ing removes a central cylindrical core of a material instead of making a hole by cutting all the metal into chips. This is particularly beneficial when working with expensive alloys as the solid cores can be used for other parts and when recycled, it’s more valuable than the “leftover” chips. The trepanning head is hollow and requires less spindle power since fewer materials are cut per revolution compared to BTA/single tube system.
Through Boring Of A Steel Billet With DHD
In order to create a deep hole, drilling through the billet is necessary. This is done using a long, thin drill bit inserted into the billet’s centre. The billet is then gently rotated as the drill bit is slowly pushed further down. As the drill bit reaches the bottom of the billet, it will create a small hole.
Once the hole has been created, a reamer can be used to enlarge the hole slightly. This will ensure that the final product has a smooth surface. Finally, a tap can be used to create threads in the bottom of the hole. This will allow for a screw or bolt to be inserted in order to secure the workpiece in place.
Counter Boring Of A Steel Billet With DHD
This is a process to enlarge the end of a pre-drilled hole by drilling out the material from inside the hole. This is done using a counterboring tool, which is a drill bit that has a cutting edge on the side as well as at the end.
The first step is to mark the area that needs to be enlarged. This is typically done with a centre punch, which makes an indentation in the material that can be seen when the drill bit is held up to it. The next step is to set the counter boring tool in a drill press.
The depth of the hole should be just slightly deeper than the length of the cutting edge on the side of the drill bit. This will ensure that the hole is enlarged evenly. The next step is to start the drill press and slowly lower the counter-boring tool into the hole.
As it reaches the bottom, pressure is applied to the side of the drill bit so it can cut through the material and continues until it reaches the desired depth. Finally, the drill bit is removed and any debris from the DHD process is cleaned up.
Deep Hole Drilling Services For Various Industries
Deep hole drilling can be used for various applications, such as enlarging the end of a pipe or creating a counterbore in a metal workpiece. This process is typically used on materials that are difficult to drill with standard drill bits, such as stainless steel or aluminium. Various sectors rely heavily on deep hole drilling services such as automotive, aerospace, defence and oil and gas. Some of the more common applications include:
- aircraft landing gear
- driveshafts
- fuel injector bodies
- fuel rails for diesel engines
- heat exchanger tube sheet
- fluid assembly ends
- steering columns
- hydraulic rams
- hydraulic cylinder inside bore
- oilfield exploration equipment
- oilfield downhole exploration
- plate rolls
- injection mould tools
Advantages Of Deep Hole Drilling Services
Gun drilling machines offer a number of advantages over traditional machining methods, including the following:
- Semi-destructive which enables repeated stress measurements at different stages
- The equipment required is portable enough to use on-site or in a laboratory
- A through-thickness bi-axial residual stress distribution is measured including stress gradients
- Incremental deep hole drilling services can measure high-magnitude residual stresses, accounting for plasticity
- Applicable to simple and complex component shapes
- Applicable to a wide range of metallic and non-metallic materials
- Counter-rotational drilling is best for accuracy
- The DHD process is fast, relative to the quantity of information produced
- The extracted cylinder of material provides a stress-free sample allowing for further tests and validations
- While DHD machines can be expensive, they do offer a high return on investment
- Deep hole drilling machines require a relatively low level of maintenance
Disadvantages Of Deep Hole Drilling Services
The main disadvantage of gun drilling is the cost as it requires a high initial investment to set up the equipment. Another downside is that the process can be time-consuming and it produces waste material that must be disposed of properly. Gun drilling can also be dangerous if not performed properly so operators must be careful when operating the machinery and workpiece.
CNC Machining And Deep Hole Drilling Services At PRV Engineering
Since the deep hole drilling process is highly specialised, it requires an engineering company that is committed to research, development, improvement and collaboration to ensure a successful project. By working with a reputable deep hole drilling provider in the UK, like PRV Engineering, you can benefit from their experience to the fullest since they can solve more complex problems.
We offer CNC and deep hole drilling services (boring services) to clients across the UK and Europe as part of an overall manufacturing project or as a sub-contracted service. As one of Europe’s top suppliers of custom fabrication, turning and milling, surface finish and deep hole drilling services, some of the sectors we work with include aerospace, defence, automotive, construction, rail, oil and gas among others.
Contact us today to discuss your project requirements or to find out more about deep hole drilling services at PRV Engineering.