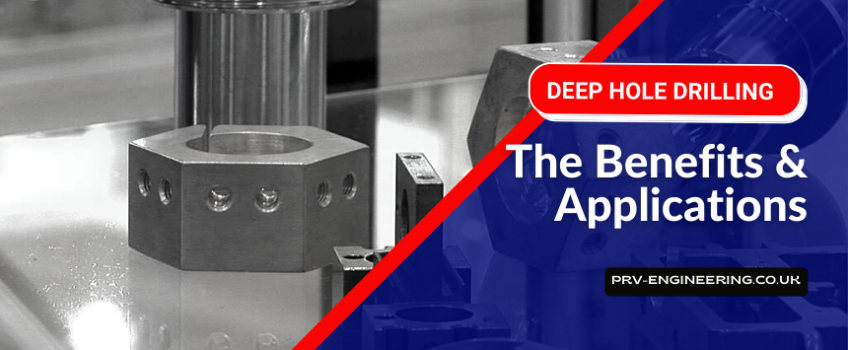
Deep hole drilling services are beneficial across several applications and require specialist equipment to maintain straightness and tolerances second to none. Oil and gas exploration equipment, armaments, aerospace equipment and engines are amongst the most common applications for deep hole drilling and machining processes.
Each of these industries needs enhanced hole qualities that are necessary for high-performance end products, such as landing gear that easily retracts. In this article, PRV explores how gun drilling works and highlights some of the benefits of quality deep hole drilling services.
Deep Hole Drilling Services And CNC Machining
It’s a given that production requires deep hole drilling services that are reliable, accurate and time-efficient. Advances in technology have allowed common CNC machining centres equipped with high-pressure through-spindle coolant to be capable of gun drilling up to a certain depth-to-diameter ratio. Other considerations are roundness and surface finish, something PRV Engineering is all too familiar with.
What Is Deep Hole Drilling And How Does It Work?
Deep hole drilling (DHD) – or deep hole machining (DHM) – is a residual stress measurement technique often referred to as gun drilling. Deep hole machining is used when a project requires high-precision round bores. It can produce holes that are within extremely tight tolerances, providing incredible accuracy compared to conventional drilling methods.
Deep hole drilling services involve the use of special tools and setups to deliver high-pressure coolant, cleanly evacuate chips while achieving depth-to-diameter holes beyond the capabilities of a typical CNC machine. This means manufacturers can reliably, accurately and efficiently achieve tolerances and production requirements.
In each of the industries that rely on deep hole drilling, the quality of the hole needs exact precision with extreme reliability. Examples of where deep hole drilling is used include the following:
- landing gear
- driveshafts
- steering columns
- hydraulic rams
- heated platens
- plate rolls
- injection mould tools
Different Types of Deep Hole Drilling
Gundrills are available in single-flute and two-flute configurations. When drilling aluminium or cast iron, two-flute gundrills are typically the preferred choice as these can be run at twice the penetration rate of single flutes. With single flute gundrilling, the machine feeds the coolant through the hole in the tool and exits along with the chips in the V-shaped groove (flute) on the drill tube.
When it comes to deep hole drilling services, there are three basic types categorised by how the cutting coolant flushes heat and chips from the surface. Below is a brief breakdown of each.
Gun drilling
The cutting tool is a fluted solid rod with a bored hole in the centre where the coolant is injected through a hole in the middle. From there it flows back outside, through the flute and brings the chips with it. Here
Single Tube System (BTA / STS)
This is only for holes with a diameter of over 15.6 mm as the tubes have a minimum size. Coolant is pumped in around the outside of the cutting tool and pushes the chips out through the centre tube.
Ejector System
This is only an acceptable technology for holes over 18.4 mm in diameter. The cutting tool is a tube within another tube where the coolant flows through the smaller one and onto the cutting face. From here the coolant and chips flow back through the larger tube.
Benefits Of Gun Drilling
As previously mentioned, deep hole drilling services achieve extremely tight tolerances which is one of the major advantages over other machining methods. And here are some more benefits of DHD:
- High cutting performance
- Minimum centreline deviation
- Exceptional drilling quality
- High process reliability through trouble-free chip removal
- Suitable for minimum quantity lubrication (MQL)
Deep Hole Drilling Services And Capabilities
Deep hole drilling services involve more than just making holes as it also includes machining, heat treatment and plating. PRV Engineering provides a wide range of Gun Drills, Ejector Drills and Counter Boring Heads which allow a number of capabilities, technical assistance and on-site drilling services.
Non-cylindrical components include holes from 5mm diameter up to 100mm diameter in any position. Centres of up to 3000mm will depend on the weight and overhang with a maximum of 4 Tonnes. Our on-site drilling services go up to 75mm in diameter and 3000mm in length. Cylindrical components involve holes from 5mm in diameter up to 200mm in any position. For centres up to 5000mm in length, the maximum weight is 4 tonnes.
Since deep hole drilling is a highly-specialised machining operation, only a select few engineering companies can perform, and PRV is one of them.
Deep Hole Drilling Services At PRV Engineering
With years of deep hole drilling experience working with a wide range of customers, PRV has unrivalled workmanship and unmatched prices. Our highly skilled and knowledgeable staff deliver only the highest levels of accuracy which is essential in terms of hole position, diametrical tolerance, surface finish and straightness.
Deep hole drilling is offered as a stand-alone service or a complete manufacturing package that provides component processes for the required stage. Using our 10 deep hole drilling machines and related equipment, we have developed a full range of supporting processes, including powder coating and 5-axis waterjet cutting among others.
Not only do we manage all your gun drilling and engineering requirements but we also deliver a “complete, customised service” all under one roof. If you have any questions about deep hole drilling or the equipment required, please chat with us on social media or contact us via the website.