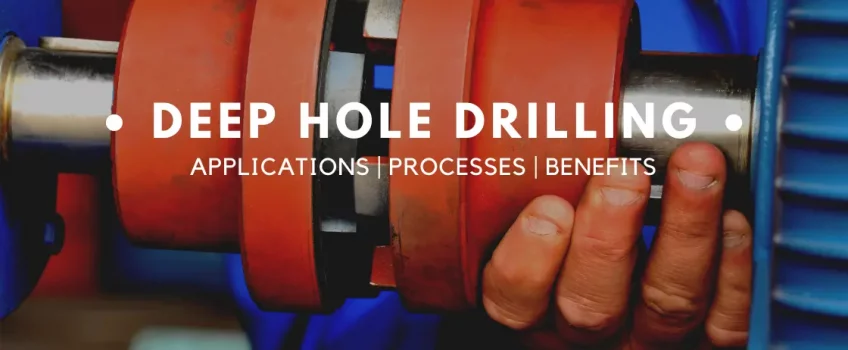
Deep hole drilling machines are metal cutting machine tools that can create very deep and extremely precise holes in just about any metal. Manufacturers relying on deep hole drilling machines can further optimise the process by using tools such as BTA and gun drills. It’s a prominent method in engineering materials and components used across numerous sectors. In this article, we take a quick look at how deep hole drilling machines work, the processes and some of the most common applications.
How Do Deep Hole Drilling Machines Work?
Deep hole drilling machines are used when a project requires high-precision round bores. It can produce holes that are within extremely tight tolerances, providing incredible accuracy compared to standard drilling methods. Using special tools and setups, these gun drilling machines deliver high-pressure coolant, and cleanly evacuate chips while achieving depth-to-diameter holes beyond the capabilities of a normal CNC machine.
This process is unique in that it can measure residual stresses at a microscopic level with a penetration of over 750 millimetres (30 inches), without completely destroying the original component. There are essentially three basic types of deep hole drilling categorised as follows:
Gun Drill Method
The cutting tool is a fluted solid rod with a bored hole in the centre where the coolant is injected through a hole in the middle. From there it flows back outside, through the flute and brings the chips with it.
Single Tube System Method
This is only for holes with a diameter of over 15.6 mm as the tubes have a minimum size. Coolant is pumped in around the outside of the cutting tool and pushes the chips out through the centre tube.
Ejector System Method
Ejector Systems are the only acceptable technology for holes over 18.4 mm in diameter. The cutting tool is a tube within another tube where the coolant flows through the smaller one and onto the cutting face. From here the coolant and chips flow back through the larger tube.
Deep Hole Drilling Processes
There are several deep hole drilling processes including BTA drilling and gun drilling with additional processes specially designed for specific tolerances. These are typically performed on BTA-style deep hole drilling machines.
What Is BTA Drilling?
BTA deep hole drilling is commonly used for larger holes, around 20 – 200 mm [0.80 – 8.00 in] in diameter with high-pressure coolant around the outside of the tool. Chips are pushed through the tool centre, drill tube and machine spindle. BTA drilling is usually 5-7 times faster than gun drilling and requires a higher power output. Counter-boring can assist BTA machines as a secondary deep hole operation to drill extended diameters.
What Is Gun Drilling?
Gun drilling, on the other hand, is used to drill smaller holes usually 1 – 50 mm (0.04 – 2.00 inches) in diameter. Once more, high-pressure coolant is introduced through the spindle and centre drill. The cutting tool is a fluted solid rod with a bored hole in the centre where the coolant is injected through a hole in the middle. From there it flows back outside, through the flute and brings the chips with it.
Common Applications Of Deel Hole Drilling Machines
Deep hole drilling machines are used in several sectors for different applications and require specialist equipment. Oil and gas exploration equipment, armaments, aerospace equipment and engines are among the most common applications but deep hole drilling machines are also used to produce surgical implants and tools. Here are some examples of where deep hole drilling machines are used:
- aircraft landing gear
- driveshafts
- fuel injector bodies
- fuel rails for diesel engines
- heat exchanger tube sheet
- fluid assembly ends
- steering columns
- hydraulic rams
- hydraulic cylinder inside bore
- oilfield exploration equipment
- oilfield downhole exploration
- plate rolls
- injection mould tools
Benefits Of Deep Hole Drilling
- Semi-destructive which enables repeated stress measurements at different stages
- The equipment required is portable enough to use on-site or in a laboratory
- A through-thickness bi-axial residual stress distribution is measured including stress gradients
- Incremental DHD can measure high magnitude residual stresses, accounting for plasticity
- Applicable to simple and complex component shapes
- Applicable to a wide range of metallic and non-metallic materials
- Counter-rotational drilling is best for accuracy
- The DHD process is fast, relative to the quantity of information produced
- The extracted cylinder of material provides a stress-free sample allowing for further tests and validations
Why Choose PRV Engineering
Not just any deep hole drilling provider can perform the required task as it is a highly specialised operation. It takes a continuous commitment to research, development, improvement and collaboration to ensure a successful project. By working with a reputable gun drilling provider, you can benefit from their experience to the fullest since they can solve more complex problems.
PRV Engineering is one of a few skilled engineering companies with a deep hole drilling facility in the UK. The service can be supplied as part of an overall manufacturing project or a sub-contracted service. As one of Europe’s top suppliers of precision engineering services, some of the sectors we work with include aerospace, defence, automotive, construction, rail, oil and gas.
We can manufacture from a customer’s own designs, specific drawings and specifications or OEM samples depending on the requirements. And, if requested, we can also provide customers with complete drawings and stress analysis calculations. If you have any questions about deep hole drilling machines or our capabilities, please contact us today.