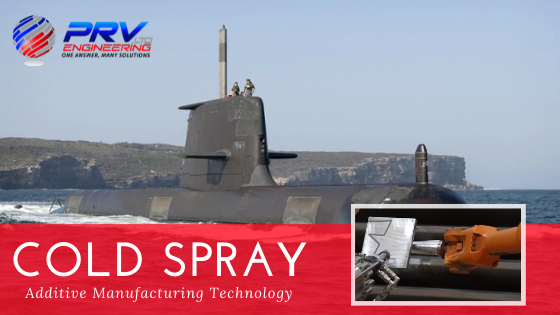
Australia’s dedicated submarine sustainment organisation, ASC, partnered with the CSIRO and DMTC Limited, has turned to cold spray 3D printing (additive manufacturing) to maintain and repair its fleet of Collins Class submarines.
Recent research and development activities focused on a few of the most challenging materials for the aircraft, space and defence industries. This includes aluminium alloys, Nickel base superalloys, different steel grades and titanium alloys.
Cold Spray Technology And The Royal Australian Navy
ASC Pty Ltd, formerly known as the Australian Submarine Corporation, is an Australian government business enterprise involved with naval shipbuilding. Headquartered in Osborne, South Australia, they have turned to cold spray technology to maintain its fleet of Collins Class submarines.
The naval fleet of any country can be deceiving as only a fraction may be active at any given time. In the case of submarines, only one in four may be on duty, with the other three either in transit, being repaired or used in training.
To keep the Royal Australian Navy up to strength, ASC is using 3D printing as part of a two-year project to speed up repairs and maintenance. The company is developing a cold spray technique that fires a spray of supersonic gas that accelerates metal powder particles to form a dense deposit on a surface.
At The Edge Of Sustainment Innovation
ASC has confirmed that their new method doesn’t need the high temperatures that other metal printing processes require. At the same time, it doesn’t damage any other components that might be nearby the immediate area.
They’ve essentially developed a way to make in situ repairs while the submarine is afloat without having to go into dry dock. Not only is this more convenient but it also means saving a massive amount of time and money.
According to ASC Chief Executive Officer Stuart Whiley: “It’s vitally important for ASC to be on the cutting edge of submarine sustainment innovation, to continually improve Australia’s submarine availability to the Royal Australian Navy service. The use of additive manufacturing for the repair of critical submarine components, including the pressure hull, will mean faster, less disruptive repairs for our frontline Collins Class submarine fleet.”
What Is Cold Spray 3D Printing?
The principle behind cold spray is based on plastic deformation of the feedstock powder particles. One could consider the implementation of cold spray technology and its benefits as a deposition process that enables the building of freeform parts and structures at very high rates.
The origins of cold spray date back to the early part of the 20th century when Thurston first developed and patented the technology. It was further investigated by Rocheville in the 1950s and rediscovered again in the 1980s at the Institute of Theoretical and Applied Mechanics of the Russian Academy of Science.
The first commercial cold spray system was introduced at the beginning of the 21st century as they started employing the cold spray process for additive repair and fabrication which can be considered as additive manufacturing.
Recommended: ‘How Does Metal 3D Printing Differ To Plastic?’
How Does Cold Spray Additive Manufacturing Work?
Cold spray technology uses pressurised carrier gas to accelerate metal powders to high velocities through a de Laval nozzle aimed at the point of deposition. As the metal powder particles collide with the part’s surface, the high kinetic energy causes plastic deformation which creates mechanical interlocking and metallurgical bonding.
While this process generates heat, it is not enough to melt the material which is a unique attribute of cold spray. This is referred to as a solid-state process that works with metals that are prone to crack during the rapid solidification which is common in most metal additive manufacturing processes. Due to the nature of the solid-state process, you can print in an open atmosphere without excessive oxidation.
Conclusion
There are two primary cold spray designs and they are high-pressure and low-pressure systems spray powder but at different velocities. The high-pressure system operates at 800 to 1,400 m/s capable of processing heavier, less ductile materials like steel and titanium alloys.
Low-pressure systems, on the other hand, operate at 300 to 600 m/s and used on lighter, ductile metals like aluminium and copper. It can use ambient air as the propellant where high-pressure systems mostly require low-weight gases like nitrogen or helium.
For more interesting reading covering topics about all things engineering, manufacturing and technology, please follow our blog. You can also join the conversation on Twitter, Facebook, YouTube or LinkedIn and remember to use the hashtag, #PRVtech
This site uses Akismet to reduce spam. Learn how your comment data is processed.
Leave a Comments